Built-Up Roofing (BUR)
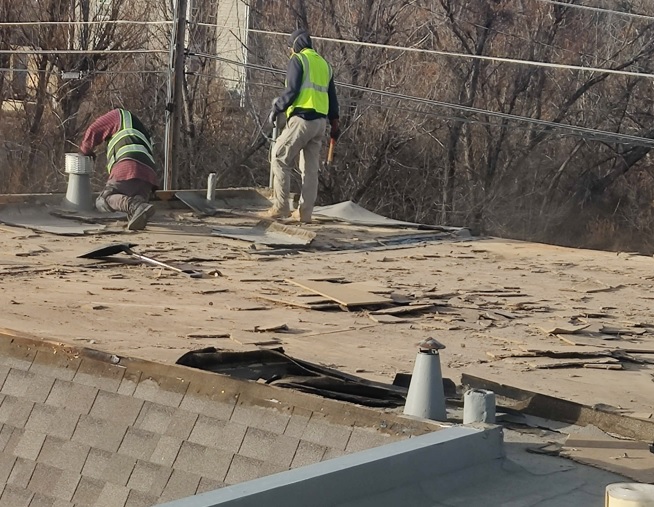
What is Built-Up Roofing?
BUR has been a reliable and trusted choice for commercial buildings for over a century. This time-tested roofing system consists of multiple layers of bitumen (asphalt) and reinforcing fabric, which are alternately applied to create a robust, waterproof membrane. The final layer is typically covered with gravel or a mineral cap sheet to provide additional protection against UV rays and the elements.
History and Evolution of BUR
Throughout its history, BUR has proven to be a durable and cost-effective solution for low-slope or flat roof structures. Its ability to withstand extreme weather conditions, including the harsh winters and intense sun we experience here in Denver, makes it a popular choice among building owners and managers. BUR systems have evolved over the years, incorporating advanced materials and installation techniques to improve performance and longevity. When you choose BUR for your commercial roof, you can have peace of mind knowing that you are investing in a system with a proven track record of success and reliability.
Advantages of BUR
When it comes to the advantages of Built-Up Roofing (BUR), durability and longevity are at the top of the list. I can confidently say that BUR systems are designed to withstand the test of time.
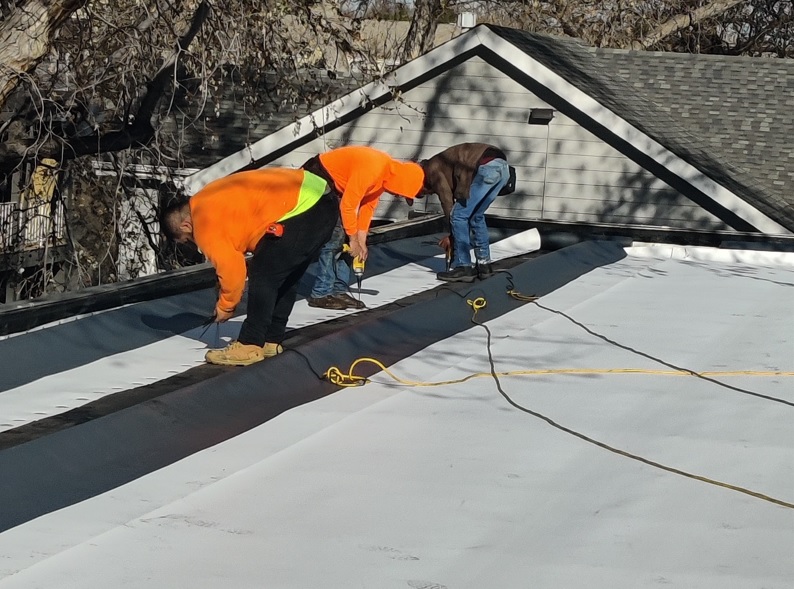
Multi-Layer Protection
When it comes to the advantages of Built-Up Roofing (BUR), durability and longevity are at the top of the list. I can confidently say that BUR systems are designed to withstand the test of time. The multi-layer protection provided by alternating layers of bitumen and reinforcing fabric creates a robust, waterproof barrier that can handle the weight of snow, the impact of hail, and the intense UV rays we experience in our region. This redundancy in layers ensures that even if one layer is damaged, the others continue to provide protection, minimizing the risk of leaks and water infiltration.
Typical Lifespan
When properly installed and maintained, a BUR system can have an impressive lifespan of 20 to 30 years, making it a wise long-term investment for your commercial property. In fact, I’ve seen well-maintained BUR roofs last even longer in some cases. By choosing a BUR system for your commercial roof, you can have confidence that your building will be protected from the elements for decades to come, saving you money on frequent repairs and replacements in the long run. We’ll provide you with a high-quality BUR installation that will stand the test of time and deliver the durability and longevity your commercial property deserves.
Weather Resistance
Our region is known for its diverse and often extreme weather conditions, from heavy snowfall and freezing temperatures in the winter to intense UV exposure and severe thunderstorms in the summer. BUR systems are engineered to withstand these challenges, providing reliable protection for your commercial property year-round.
The multiple layers of bitumen and reinforcing fabric in a BUR system create a thick, durable barrier that can handle the weight of snow and ice without cracking or compromising the roof’s integrity. This is crucial in our area, where snow can accumulate quickly and put significant stress on a roof. Additionally, the gravel or mineral cap sheet layer of a BUR system helps protect the underlying layers from UV degradation, which is essential given the high altitude and intense sunlight we experience in Denver.
When it comes to rain and moisture, BUR systems excel in preventing leaks and water infiltration. The redundant layers of waterproofing ensure that even if one layer is damaged, the others continue to provide protection, minimizing the risk of leaks and costly water damage to your building’s interior. I have seen firsthand how BUR systems have performed exceptionally well in the face of our region’s severe weather events, from hail storms to heavy downpours.
By choosing a BUR system for your commercial roof, you can have peace of mind knowing that your building is protected by a roofing solution that is specifically designed to withstand the unique weather challenges we face in Denver. I am confident that a properly installed and maintained BUR system will provide your property with the weather resistance it needs to stay safe, dry, and protected for years to come.
Cost-Effectiveness
I understand that cost is a significant factor when choosing a roofing system for your property. While the initial installation cost of a Built-Up Roofing (BUR) system may be higher compared to some other roofing options, I believe that the long-term savings on maintenance and repairs make BUR a cost-effective choice for many commercial building owners.
When you invest in a BUR system, you are investing in a roofing solution that is built to last. The durability and longevity of BUR mean that you can expect fewer repairs and less frequent replacements over the life of your roof. This translates to significant savings on maintenance costs down the line, as you won’t have to spend money on constant repairs or premature replacement.
The energy efficiency of BUR systems can lead to additional savings on your building’s heating and cooling costs. The reflective properties of the gravel or mineral cap sheet layer can help reduce heat absorption, keeping your building cooler in the summer and reducing the strain on your HVAC system. This not only saves you money on energy bills but also promotes a more comfortable environment for your building’s occupants.
A high-quality BUR installation will maximize your long-term savings. By using premium materials and adhering to industry best practices, we ensure that your BUR roof will perform optimally for decades, minimizing the need for costly repairs and saving you money in the long run. When you factor in the long-term savings and energy efficiency benefits, I believe that a BUR system is a smart, cost-effective choice for your commercial property here in Denver.
Energy Efficiency
In our region, where we experience both cold winters and hot summers, the insulation properties of your roofing system play a crucial role in regulating your building’s temperature and reducing your energy consumption.
BUR systems offer excellent insulation properties due to their multi-layer construction. The alternating layers of bitumen and reinforcing fabric create a thick, dense barrier that helps prevent heat transfer between your building’s interior and the external environment. In the winter, this means that a BUR system can help keep heat inside your building, reducing the burden on your heating system and saving you money on energy bills. During the summer months, the insulating properties of BUR work to keep the heat out, maintaining a cooler interior temperature and easing the load on your air conditioning system.
In addition to the inherent insulation properties of BUR, the final layer of gravel or mineral cap sheet can further enhance energy efficiency by reflecting sunlight and heat away from your building. This reflective surface minimizes heat absorption, which is especially beneficial in our Denver climate, where we have many sunny days throughout the year. By reducing the amount of heat that enters your building through the roof, a BUR system can help you maintain a more consistent and comfortable indoor temperature while also potentially lowering your cooling costs.
By installing a well-designed and properly maintained BUR system, you can expect to see significant energy savings over the life of your roof. These savings not only benefit your bottom line but also contribute to a reduced environmental impact and a more sustainable future for our community. Let’s work together to explore how a BUR system can improve the energy efficiency of your commercial building here in Denver.
Ease of Repair and Maintenance
Ease of repair and maintenance is a key consideration when choosing a roofing system for your property. One of the significant advantages of Built-Up Roofing (BUR) systems is the simplicity of spot repairs, which can save you time and money over the life of your roof.
In the event that your BUR system sustains localized damage, such as a puncture or a small crack, the repair process is relatively straightforward. The multi-layer construction of BUR allows for targeted repairs without the need to replace the entire roof. Our experienced technicians can quickly identify the damaged area, remove the affected layers, and patch the spot with new bitumen and reinforcing fabric. This localized approach to repairs minimizes disruption to your business operations and helps maintain the overall integrity of your roofing system.
While BUR systems are known for their durability and longevity, regular maintenance is still essential to ensure optimal performance and extend the life of your roof. We recommend scheduling annual inspections and performing routine maintenance tasks, such as cleaning drains, removing debris, and checking for any signs of wear or damage. By proactively addressing minor issues and conducting regular maintenance, you can prevent more serious problems from developing and maximize the lifespan of your BUR roof.
Our team of skilled professionals is dedicated to providing you with exceptional maintenance and repair services tailored to your specific needs. We use high-quality materials and adhere to industry best practices to ensure that your BUR system continues to perform at its best. By partnering with us for your roofing maintenance and repair needs, you can have peace of mind knowing that your commercial property in Denver is protected by a well-maintained and efficiently repaired BUR system, ultimately saving you time and money in the long run.
Components of BUR
As a commercial roofing company owner in Denver, Colorado, I believe it’s essential for my clients to understand the various components that make up a Built-Up Roofing (BUR) system. One of the critical components is the base sheet, which serves as the foundation for the entire roofing system.
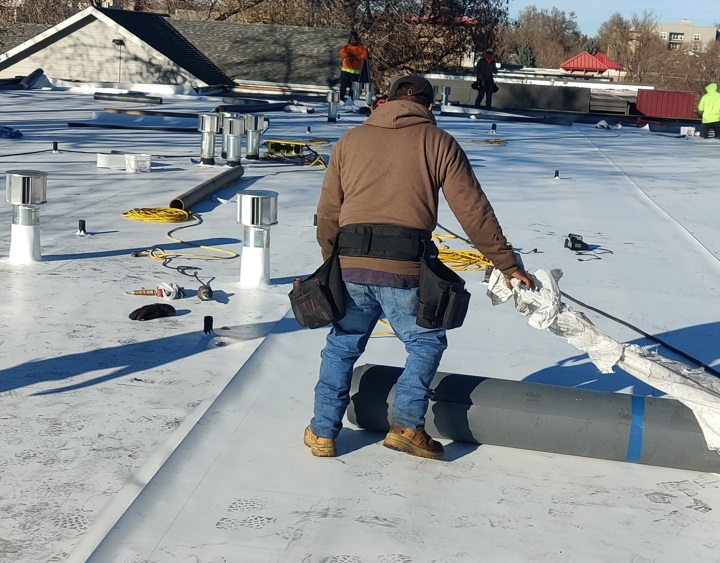
Base Sheets
Base sheets are the first layer installed directly onto the roof deck or insulation, and they play a vital role in the overall performance and longevity of your BUR system. There are several types of base sheets commonly used in BUR installations, including organic felts, asphalt-coated fiberglass sheets, and modified bitumen sheets. The choice of base sheet depends on factors such as the specific project requirements, local building codes, and the preferences of the building owner or architect.
The primary purpose of the base sheet is to provide a stable, uniform surface for the subsequent layers of bitumen and reinforcing fabric. It helps to smooth out any irregularities or imperfections in the roof deck, creating a level surface that promotes proper adhesion and drainage. Additionally, base sheets act as a secondary water-resistant barrier, providing an extra layer of protection against moisture infiltration.
In my experience, using high-quality base sheets is crucial to the long-term performance of a BUR system. Inferior base sheets can lead to premature deterioration, compromising the integrity of the entire roof. That’s why my team and I only use trusted, industry-approved base sheets from reputable manufacturers. We understand that the base sheet is the foundation upon which the rest of the BUR system relies, and we take great care to ensure that this component is installed correctly and with the utmost attention to detail.
When you choose our commercial roofing company for your BUR installation in Denver, you can have confidence knowing that we prioritize the use of premium base sheets to provide your building with a strong, reliable foundation for a long-lasting, high-performing roofing system.
Ply Sheets
Ply sheets are the layers of reinforcing fabric that are alternated with layers of bitumen to create the main waterproofing and protective component of the BUR system.
Ply sheets are typically composed of organic or fiberglass materials, which provide strength, stability, and durability to the roofing system. These sheets are designed to absorb and reinforce the bitumen, creating a cohesive, watertight membrane that can withstand the elements and protect your building from moisture intrusion.
The number of ply sheets used in a BUR system can vary depending on the specific project requirements, local building codes, and the desired level of durability. In general, a higher number of ply sheets will result in a thicker, more robust roofing system that can better withstand the test of time. Most BUR systems consist of three to five ply sheets, but in some cases, up to seven or more sheets may be used for added strength and longevity.
I always recommend using a sufficient number of high-quality ply sheets to ensure the long-term performance and durability of your BUR system. My team and I carefully select ply sheets from reputable manufacturers and adhere to industry best practices during installation to create a seamless, reliable waterproofing membrane.
The ply sheets’ composition and the number of layers used directly impact the durability and life expectancy of your BUR system. By investing in a well-designed BUR system with an appropriate number of high-quality ply sheets, you can have peace of mind knowing that your commercial property in Denver is protected by a roofing solution that is built to last, saving you money on repairs and replacements in the long run.
Bitumen
Bitumen is the waterproofing agent that binds the layers of ply sheets together, creating a cohesive, watertight membrane that protects your building from the elements.
There are two main types of bitumen used in BUR systems: asphalt and coal tar. Asphalt is the more common choice in modern BUR installations due to its versatility, affordability, and ease of application. It is derived from petroleum and is known for its excellent waterproofing properties and flexibility. Coal tar, on the other hand, is a byproduct of the coal distillation process and is known for its exceptional resistance to water, chemicals, and UV rays. However, coal tar has largely fallen out of use in recent years due to health and environmental concerns.
When it comes to the application of bitumen in a BUR system, there are two primary methods: hot applied and cold applied. Hot applied bitumen is heated to high temperatures (usually between 350°F and 400°F) and then mopped or squeegeed onto the roof surface, where it bonds with the ply sheets as it cools. This method allows for a strong, seamless bond between the layers and is the most common application method for BUR systems.
Cold applied bitumen, also known as cold process adhesive, is a newer technology that allows for the application of bitumen without the need for heating. This method involves the use of a solvent-based or emulsion-based adhesive that is applied at ambient temperatures. Cold applied systems can be useful in situations where hot applied methods are not practical or safe, such as in occupied buildings or areas with limited access to heating equipment.
My team and I have extensive experience working with both hot applied and cold applied bitumen systems. We carefully consider factors such as your building’s specific needs, local climate, and environmental concerns when recommending the most appropriate type of bitumen and application method for your BUR system. By selecting the right bitumen and application technique, we can ensure that your commercial property in Denver is protected by a high-quality, long-lasting roofing solution that meets your unique requirements.
Surfacing Materials
The surfacing material is the final layer applied to the top of the BUR membrane, and it serves several critical functions, including protecting the underlying layers from UV damage, improving fire resistance, and enhancing the aesthetic appearance of your roof.
One of the most common surfacing materials for BUR systems is gravel. Gravel is an affordable and effective option that provides excellent protection against UV rays, which can degrade the bitumen and cause premature aging of your roof. The gravel also helps to improve fire resistance, as it creates a non-combustible surface that can prevent the spread of flames. Additionally, gravel can help to distribute weight evenly across the roof surface, reducing the risk of punctures or damage from foot traffic.
Another popular surfacing option is asphalt. Asphalt surfacing involves applying a layer of hot asphalt over the top of the BUR membrane, followed by a layer of mineral granules. This method provides a sleek, uniform appearance and offers excellent UV protection. Asphalt surfacing is also highly durable and can help to extend the life of your BUR system.
For building owners looking to maximize energy efficiency and reduce cooling costs, reflective coatings are an increasingly popular choice. These coatings are applied as a liquid and form a seamless, highly reflective surface that helps to reflect sunlight and heat away from your building. By reducing heat absorption, reflective coatings can help to lower interior temperatures, reduce the strain on your HVAC system, and potentially lead to significant energy savings over time.
We’ll work closely with you to determine the best surfacing material for your specific needs and budget. We take into account factors such as your building’s location, climate, and energy efficiency goals when recommending a surfacing option. Whether you choose gravel, asphalt, or a reflective coating, you can have confidence knowing that your commercial property in Denver is protected by a high-quality, durable BUR system that is tailored to your unique requirements.
Installation Process
Proper preparation is critical when installing a Built-Up Roofing (BUR) system. The success and longevity of your new roof depend heavily on the condition of the existing roof substrate and the steps taken to prepare it for the new installation.
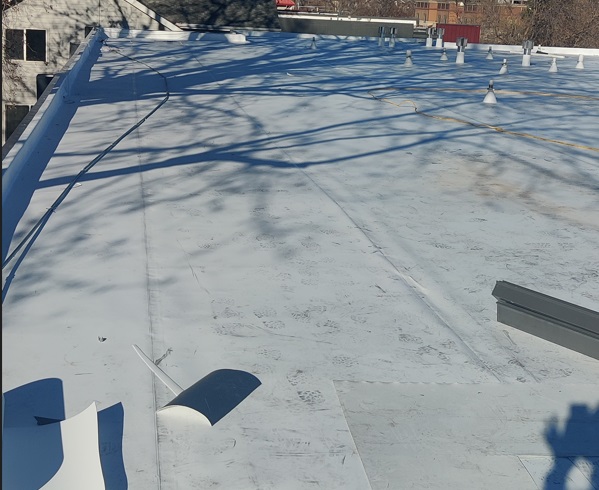
Preparation
Before we begin any BUR installation project, my team and I conduct a thorough inspection of your existing roof. This inspection allows us to assess the overall condition of the roof deck, identify any areas of damage or deterioration, and determine if any repairs or replacements are necessary before proceeding with the new installation. By addressing these issues upfront, we can ensure that your new BUR system has a solid, stable foundation upon which to be built.
Once the inspection is complete and any necessary repairs have been made, we move on to the cleaning and priming phase. This step is critical, as it helps to ensure proper adhesion between the new BUR system and the existing roof substrate. We begin by thoroughly cleaning the roof surface to remove any dirt, debris, or contaminants that could interfere with the bonding process. This may involve the use of power washers, brooms, or other specialized cleaning equipment, depending on the condition of the roof.
After cleaning, we apply a primer to the roof surface. The primer is a specially formulated adhesive that helps to create a strong, durable bond between the existing roof substrate and the new BUR system. The type of primer used will depend on the specific materials involved and the condition of the roof. My team and I have extensive experience working with a variety of primers and will select the best option for your unique situation.
By taking the time to properly inspect, clean, and prime your existing roof, we can help to ensure that your new BUR system will provide long-lasting, reliable protection for your commercial property in Denver. We provide the highest level of craftsmanship and attention to detail throughout the entire installation process, starting with these critical preparation steps.
Layering Process
The layering process is the heart of the BUR installation, and it’s where the various components come together to create a durable, waterproof membrane that will protect your building for years to come.
Once the roof substrate has been properly prepared, cleaned, and primed, we begin the layering process by installing the base sheets. The base sheets are the foundation of the BUR system, and they provide a stable, uniform surface for the subsequent layers. My team and I carefully apply the base sheets to the roof substrate, ensuring that they are smooth, wrinkle-free, and properly adhered.
With the base sheets in place, we move on to the alternating layers of ply sheets and bitumen. This is where the real magic happens. We start by applying a layer of hot bitumen to the base sheet using a mop or mechanical spreader. While the bitumen is still hot, we embed a layer of ply sheet into it, making sure that it is fully saturated and free of any air pockets or voids. We then apply another layer of hot bitumen on top of the ply sheet, and the process repeats.
The number of alternating layers of ply sheets and bitumen will depend on the specific design of your BUR system, but a typical installation will include three to five layers. As we build up these layers, the BUR membrane becomes increasingly strong, durable, and resistant to water, UV rays, and other environmental stressors.
Once the final layer of bitumen has been applied, we install the surfacing material of your choice. Whether you opt for gravel, asphalt, or a reflective coating, the surfacing material serves to protect the underlying layers, improve fire resistance, and enhance the aesthetic appearance of your roof.
Throughout the layering process, my team and I maintain the highest standards of quality and attention to detail. We understand that even the smallest imperfections can compromise the integrity of the BUR system, so we take great care to ensure that each layer is installed flawlessly. By the time we’re finished, you can have confidence knowing that your commercial property in Denver is protected by a top-quality BUR system that will provide reliable, long-lasting performance.
Timeframe
One of the most common questions I hear from clients is, “How long will it take to install my new Built-Up Roofing (BUR) system?” The answer to this question can vary depending on a number of factors, but I always strive to provide my clients with a clear, realistic timeline for their project.
In general, the installation of a BUR system can take anywhere from a few days to several weeks, depending on the size and complexity of the project. For a typical commercial roof, you can expect the installation process to take between 1-2 weeks from start to finish. However, it’s important to keep in mind that this is just a rough estimate, and the actual timeline may be shorter or longer based on the specific circumstances of your project.
One of the biggest factors that can impact the duration of a BUR installation is the size of your roof. Larger roofs naturally take longer to complete, as there is more surface area to cover and more materials to install. The complexity of your roof design can also play a role, as roofs with multiple levels, drainage systems, or penetrations may require additional time and attention to detail.
Weather conditions are another important factor that can affect the timeline of your BUR installation. In Denver, we are fortunate to have a relatively mild climate that allows for roofing work to be performed year-round. However, we can still experience periods of inclement weather, such as heavy rain, snow, or high winds, which can delay the installation process. My team and I always prioritize the safety of our workers and the quality of our workmanship, so we may need to adjust the timeline to accommodate for weather-related disruptions.
Other factors that can impact the duration of your BUR installation include the availability of materials, the size of the installation crew, and any unforeseen issues that may arise during the project. As your trusted local roofing expert, I will work closely with you to develop a detailed project plan that takes all of these factors into account, so you can have a clear understanding of what to expect in terms of timeline and progress.
At the end of the day, my goal is to provide you with a high-quality, long-lasting BUR system that meets your specific needs and exceeds your expectations. While the installation process may take some time, I assure you that the end result will be well worth the wait.
Considerations for BUR in Denver, Colorado
When it comes to selecting a roofing system for your commercial property, it’s essential to choose one that can withstand the specific weather conditions we face here in Denver, and I can confidently say that BUR is an excellent choice..
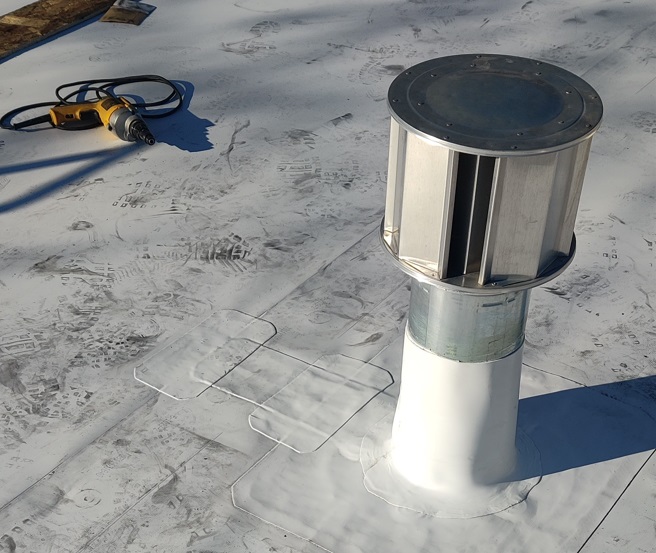
Climate Adaptability
One of the biggest advantages of BUR systems is their exceptional performance in both cold winters and hot summers. Denver is known for its harsh winter weather, with temperatures often dropping well below freezing and heavy snowfall accumulating on rooftops. BUR systems are designed to withstand these conditions, thanks to their multiple layers of bitumen and reinforcing fabric. The redundancy provided by these layers helps to prevent cracking, splitting, and other forms of damage that can occur as a result of extreme cold and the weight of snow and ice.
On the other end of the spectrum, Denver summers can be intensely hot, with temperatures soaring into the 90s and even reaching triple digits on occasion. This intense heat can cause some roofing materials to break down and deteriorate over time, leading to premature failure and the need for costly repairs or replacement. However, BUR systems are highly resistant to heat and UV radiation, thanks to the reflective surfacing options available, such as gravel or reflective coatings. By reflecting sunlight and heat away from the building, these surfacing materials help to keep the roof surface cooler, which in turn helps to extend the lifespan of the BUR system and improve energy efficiency.
Another factor to consider when it comes to BUR performance in Denver is our high altitude. At over 5,000 feet above sea level, the air is thinner and the UV radiation is more intense than at lower elevations. This can accelerate the aging process of some roofing materials, but BUR systems are well-suited to these conditions. The multiple layers of bitumen and reinforcing fabric provide excellent protection against UV damage, and the gravel or reflective surfacing options help to further shield the underlying layers from the sun’s harmful rays.
BUR systems perform well in Denver’s challenging climate. With proper design, installation, and maintenance, a BUR system can provide your commercial property with reliable, long-lasting protection against the elements, no matter what Mother Nature throws our way.
Environmental Factors
There are two key considerations that I always discuss with my clients: energy efficiency and UV resistance at high altitudes.
At an elevation of over 5,000 feet above sea level, Denver’s high altitude presents both challenges and opportunities when it comes to energy efficiency. On one hand, the thinner air and increased solar radiation at high elevations can lead to greater heat gain and cooling loads for buildings. This means that your roofing system plays a critical role in regulating the temperature and energy efficiency of your property. Fortunately, BUR systems offer excellent insulation properties that can help to mitigate these effects. By incorporating high-quality insulation materials and reflective surfacing options, such as white gravel or reflective coatings, we can help to reduce heat absorption and improve the overall energy efficiency of your building.
In addition to energy efficiency, UV resistance is another crucial factor to consider when selecting a roofing system for your Denver commercial property. At high elevations, the atmosphere filters out less UV radiation, which means that your roof is exposed to higher levels of UV light than it would be at lower elevations. Over time, this increased UV exposure can lead to premature aging, cracking, and deterioration of some roofing materials. However, BUR systems are highly resistant to UV damage, thanks to the multiple layers of bitumen and reinforcing fabric that provide a strong, stable barrier against the sun’s harmful rays. By selecting a BUR system with a UV-resistant surfacing option, such as white gravel or a reflective coating, we can further enhance the UV protection of your roof and extend its lifespan.
We have extensive experience designing and installing BUR systems that are optimized for Denver’s unique environmental conditions. I take a comprehensive approach to every project, considering factors such as building orientation, shading, and ventilation to create a customized solution that maximizes energy efficiency and UV resistance. By investing in a high-quality BUR system that is tailored to your specific needs and environment, you can enjoy long-lasting protection, improved building performance, and reduced operating costs over the life of your roof.
When you choose my company for your commercial roofing needs, you can have confidence knowing that your BUR system will be designed and installed with the utmost attention to detail and a deep understanding of the environmental factors that impact roofing performance in Denver. Whether you are looking to improve the energy efficiency of your building, extend the lifespan of your roof, or both, I am committed to delivering a solution that exceeds your expectations and provides lasting value for your commercial property.
Local Building Codes and Regulations
One of our top priorities is ensuring that every roofing project we undertake is fully compliant with local building codes and regulations. When it comes to installing a Built-Up Roofing (BUR) system on your commercial property, there are several key standards and requirements that we must adhere to in order to meet Denver’s stringent building codes.
First and foremost, all roofing materials used in a BUR system must be approved by the Denver Building Department and meet the specifications outlined in the International Building Code (IBC). This includes the base sheets, ply sheets, bitumen, and surfacing materials. As your roofing contractor, it is my responsibility to select materials that not only meet these standards but also provide the highest level of quality and performance for your specific project.
In addition to material requirements, Denver building codes also dictate certain installation practices and techniques that must be followed to ensure the integrity and safety of the roofing system. For example, the codes specify minimum slope requirements for proper drainage, as well as guidelines for flashing, ventilation, and other critical components of the roof assembly. My team and I are fully versed in these requirements and take great care to implement them on every BUR installation we perform.
Another important aspect of compliance with Denver building standards is obtaining the necessary permits and inspections. Before we begin any roofing work, we will secure all required permits from the Denver Building Department, which may include a general building permit, a roofing permit, and/or an HVAC permit, depending on the scope of the project. Throughout the installation process, we will schedule inspections with city officials to verify that our work meets all applicable codes and standards.
I take great pride in my team’s ability to navigate the complex landscape of Denver building codes and regulations. We stay up-to-date on all the latest requirements and best practices, and we are committed to delivering a finished product that not only meets but exceeds the standards set forth by the city.
When you choose my company for your BUR installation, you can have peace of mind knowing that your project will be completed in full compliance with Denver building standards. This not only ensures the safety and longevity of your roofing system but also protects your investment and helps to maintain the value of your commercial property over time.
Maintenance and Inspection of BUR
I cannot stress enough the importance of regular maintenance and inspections for your Built-Up Roofing (BUR) system. While BUR systems are known for their durability and long-lasting performance, they still require ongoing care and attention to ensure that they continue to provide optimal protection for your commercial property. That’s why I always recommend that my clients implement a routine inspection schedule to catch potential issues early and extend the life of their roofing investment.
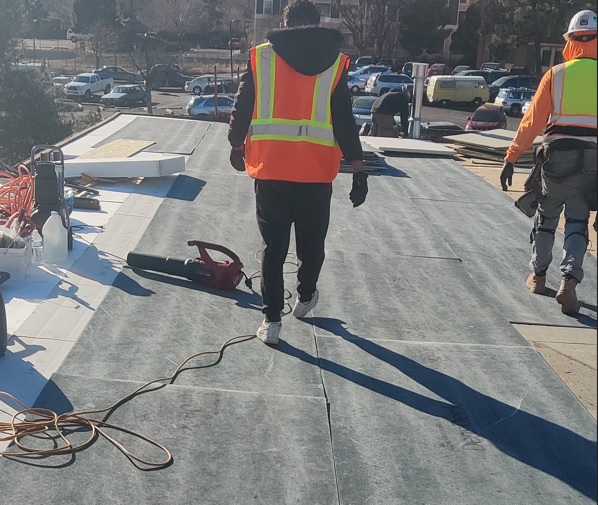
Routine Inspections
So, how often should you have your BUR system inspected? As a general rule of thumb, I recommend that commercial property owners schedule professional inspections at least twice a year – once in the spring and once in the fall. These regular check-ups allow us to assess the condition of your roof after the harsh winter months and intense summer heat, respectively. However, if your property is located in an area with more extreme weather conditions or if your roof is older, you may want to consider increasing the frequency of inspections to quarterly or even monthly.
During a routine inspection, my team and I will thoroughly examine all aspects of your BUR system, paying close attention to several key areas. First and foremost, we will check for any signs of physical damage, such as cracks, blisters, or punctures in the membrane. These issues can allow water to penetrate the roof and cause leaks, so it’s important to identify and repair them as soon as possible. We will also inspect the flashing around chimneys, vents, and other penetrations to ensure that it is properly sealed and secured.
Another critical area of focus during our inspections is drainage. Over time, debris can accumulate on your roof and clog drains or gutters, leading to ponding water that can damage your BUR system. We will clean out any debris and check to make sure that water is flowing freely off the roof and away from your building.
Finally, we will assess the overall condition of your BUR system’s surfacing material, whether it be gravel, asphalt, or a reflective coating. We will look for any signs of erosion, bare spots, or other wear and tear that may indicate the need for resurfacing or repair.
By conducting these routine inspections and addressing any issues that arise, we can help you maximize the lifespan of your BUR system and avoid costly repairs or premature replacement down the road. I am committed to providing you with the highest level of service and support throughout the life of your roofing investment. When you choose my company for your BUR maintenance and inspection needs, you can have peace of mind knowing that your commercial property is in good hands.
Preventive Maintenance
Preventive maintenance is key to extending the life of your Built-Up Roofing (BUR) system and avoiding costly repairs down the line. While routine inspections are essential for identifying potential issues, it’s equally important to take a proactive approach to maintaining your roof on a regular basis. That’s why I always recommend that my clients implement a preventive maintenance plan that includes regular cleaning, debris removal, and timely sealing and patching of small cracks.
One of the most critical aspects of preventive maintenance for your BUR system is keeping the roof surface clean and free of debris. Over time, leaves, branches, and other organic matter can accumulate on your roof, trapping moisture and promoting the growth of algae and moss. If left unchecked, this debris can cause damage to your roofing membrane, leading to leaks and other issues. To prevent this, I recommend that you schedule regular cleaning and debris removal at least twice a year, or more frequently if your property is located near trees or other sources of debris.
In addition to regular cleaning, it’s also important to promptly address any small cracks or damage to your BUR system as soon as they are identified. Even minor cracks or punctures can allow water to penetrate the roof and cause significant damage over time. By sealing and patching these issues promptly, you can prevent them from turning into larger, more expensive problems down the road.
My team and I use specialized materials and techniques to seal and patch small cracks in BUR systems, ensuring a durable and long-lasting repair. We start by thoroughly cleaning the affected area and allowing it to dry completely. Then, we apply a high-quality sealant or patching compound that is specifically designed for use on BUR systems. We smooth the sealant or patch to create a seamless, waterproof barrier and allow it to cure fully before applying any additional coatings or surfacing materials.
By implementing a regular preventive maintenance plan that includes cleaning, debris removal, and prompt sealing and patching of small cracks, you can significantly extend the life of your BUR system and avoid costly repairs or premature replacement. As your trusted local roofing expert, I am committed to helping you develop a customized maintenance plan that meets the unique needs of your commercial property and budget.
When you choose my company for your BUR preventive maintenance needs, you can have confidence knowing that your roof is in the hands of experienced professionals who are dedicated to protecting your investment and ensuring the long-term performance of your roofing system. Whether you need a one-time cleaning and repair service or ongoing maintenance support, I am here to help you keep your BUR system in top condition for years to come.
Handling Repairs
Even with regular maintenance and inspections, repairs may still be necessary from time to time to keep your Built-Up Roofing (BUR) system performing at its best. The key to minimizing the impact of repairs on your business and budget is identifying damage early and using effective repair techniques that address the root cause of the problem.
When it comes to identifying damage early, there are a few key signs that my team and I look for during our inspections. These include visible cracks or splits in the roofing membrane, areas of standing water or ponding, and any signs of blistering or bubbling on the roof surface. We also pay close attention to the condition of flashing and other critical components of your roofing system, as these areas are often the first to show signs of wear or damage.
If we do identify any issues during our inspection, we will work with you to develop a customized repair plan that addresses the specific needs of your BUR system. Our repair techniques are designed to be effective, long-lasting, and minimally disruptive to your business operations.
One of the most common repair techniques we use for BUR systems is a three-course repair. This involves applying three layers of roofing materials to the damaged area – a layer of roofing cement, a layer of reinforcing fabric, and another layer of roofing cement. This approach creates a strong, durable patch that is fully integrated with the existing roofing membrane.
For larger or more complex repairs, we may use a full-ply replacement technique. This involves cutting out the damaged area of the roofing membrane and replacing it with a new section of ply sheet and bitumen. We take great care to ensure that the new section is properly sealed and integrated with the surrounding roofing materials to prevent future leaks or damage.
Regardless of the specific repair technique we use, our goal is always to provide a long-lasting, effective solution that protects your investment and extends the life of your BUR system. We use only the highest-quality materials and industry-leading techniques to ensure that your repairs are done right the first time.
Whether you need a minor repair or a more extensive overhaul, my team and I are here to provide the expert guidance and support you need to make informed decisions about your roofing investment. When you choose my company for your BUR repair needs, you can have confidence knowing that your commercial property is in the hands of experienced professionals who are dedicated to your success.
Cost of BUR
One of the most common questions I receive from clients is about the cost of installing a Built-Up Roofing (BUR) system. While the initial installation cost of a BUR system can be higher than some other roofing options, it’s important to understand that there are several factors that can influence the overall cost of your project.
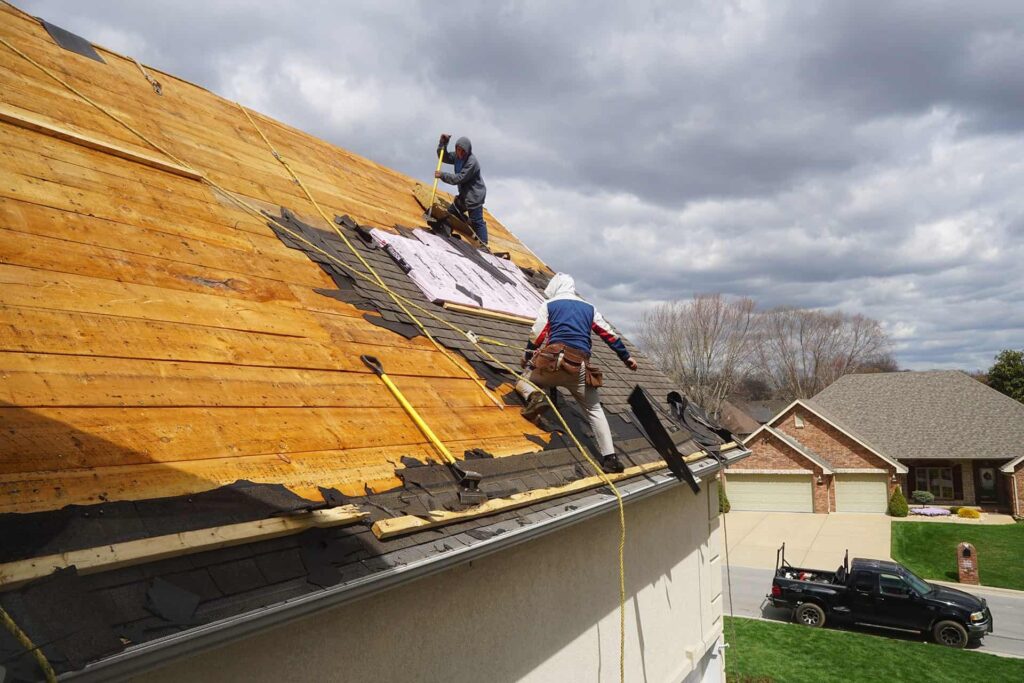
Initial Installation Costs
The first and most obvious factor that impacts the cost of a BUR installation is the size of your roof. Simply put, the larger your roof, the more materials and labor will be required to complete the installation, which will drive up the overall cost of the project. However, it’s important to note that larger roofs may also provide opportunities for economies of scale, which can help to reduce the cost per square foot.
Another key factor that can influence the cost of your BUR installation is the complexity of your roof design. Roofs with multiple levels, steep slopes, or numerous penetrations (such as vents or skylights) will require more time and specialized labor to install, which can increase the overall cost of the project. Additionally, if your roof requires any special reinforcement or structural modifications to support the weight of a BUR system, this can also add to the overall cost.
Finally, the specific materials used in your BUR system can also impact the cost of installation. While traditional BUR systems use a combination of bitumen and gravel, there are now a variety of modified bitumen and single-ply membranes that can be used in BUR installations. These materials can offer enhanced performance and durability, but they may also come with a higher price tag.
As a building owner or manager, it’s important to work with an experienced roofing contractor who can help you navigate these various factors and develop a customized BUR solution that meets your specific needs and budget. At my company, we pride ourselves on providing transparent, detailed cost estimates that take into account all of the unique factors of your project. We’ll work with you to identify opportunities for cost savings without compromising on quality or performance, and we’ll provide you with a clear understanding of the long-term value and benefits of your BUR investment.
Ultimately, while the initial installation cost of a BUR system may be higher than some other roofing options, it’s important to consider the long-term cost-effectiveness of this proven and reliable roofing solution. With proper maintenance and care, a BUR system can provide decades of reliable protection for your commercial property, offering an excellent return on investment over the life of your roof.
Long-Term Costs
It’s essential to consider not just the initial installation cost of a Built-Up Roofing (BUR) system, but also the long-term costs associated with maintaining and repairing the roof over its lifespan. While a BUR system can offer excellent durability and longevity, it’s important to understand that regular maintenance and occasional repairs will be necessary to keep your roof performing at its best.
When it comes to maintenance expenses, the good news is that BUR systems typically require less frequent maintenance than some other roofing options. However, it’s still important to budget for regular inspections and preventive maintenance to identify and address any potential issues before they become more serious problems. We recommend scheduling annual or semi-annual inspections to assess the condition of your BUR system and perform any necessary cleaning, debris removal, or minor repairs. These proactive maintenance measures can help to extend the life of your roof and minimize the need for more costly repairs down the line.
Of course, even with regular maintenance, repairs may still be necessary from time to time to address specific issues or damage to your BUR system. The cost of these repairs can vary depending on the extent and complexity of the damage, as well as the specific materials and techniques required to complete the repair. In some cases, localized repairs may be sufficient to address minor issues like small cracks or punctures in the roofing membrane. However, more extensive damage may require a full replacement of one or more roofing plies, which can be a more significant expense.
When weighing the costs of repairs versus replacement, it’s important to consider the age and overall condition of your BUR system, as well as your long-term plans for the building. If your roof is relatively new and in good condition overall, investing in repairs may be the most cost-effective option to extend the life of the roof. However, if your roof is nearing the end of its expected lifespan or has extensive damage that would be costly to repair, a full replacement may be the more prudent choice.
We’ll help you navigate these complex decisions and develop a long-term roofing strategy that balances your performance needs with your budget realities. We pride ourselves on providing honest, transparent advice and recommendations based on a thorough assessment of your unique situation. Working with you to identify the most cost-effective solution for your needs, whether that’s a targeted repair, a full replacement, or a proactive maintenance plan to extend the life of your existing BUR system.
Ultimately, while the long-term costs of maintaining and repairing a BUR system are an important consideration, it’s also essential to recognize the value and peace of mind that comes with investing in a proven, reliable roofing solution. With proper care and maintenance, a BUR system can provide decades of protection for your commercial property, offering an excellent return on investment over the life of your roof.