Elastomeric Roof Coating
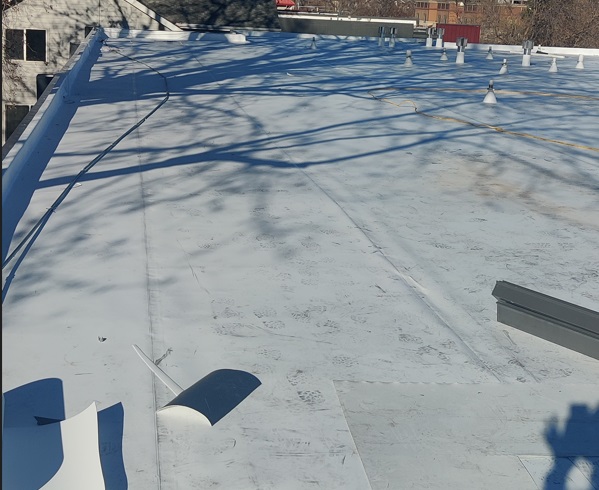
What is Elastomeric Roof Coating?
Elastomeric coatings have become an invaluable tool in my arsenal for extending the life of existing commercial roof systems. These liquid-applied membranes can be brushed, rolled or sprayed directly over an aging roof to form a thick, seamless, flexible surface that restores the rooftop’s waterproofing capabilities. Elastomeric coatings are highly advantageous because they can protect a wide variety of roof substrates – from metal and single-ply membranes to built-up asphalt and modified bitumen
Reliable & Flexible
Rather than go through the disruption and expense of a total roof replacement, a quality elastomeric roof restoration provides a reliable, long-term solution to seal leaks and add years of service life at a fraction of the cost. The coatings’ outstanding flexibility and elongation properties allow them to stretch and recover their shape, bridging cracks and accommodating roof movement to prevent future leaks. For property managers dealing with limited budgets and operational disruptions, elastomeric coatings offer a smart, sustainable option to maximize their roofing investment while minimizing overhead expenses.
Advantages of Elastomeric Roof Coatings
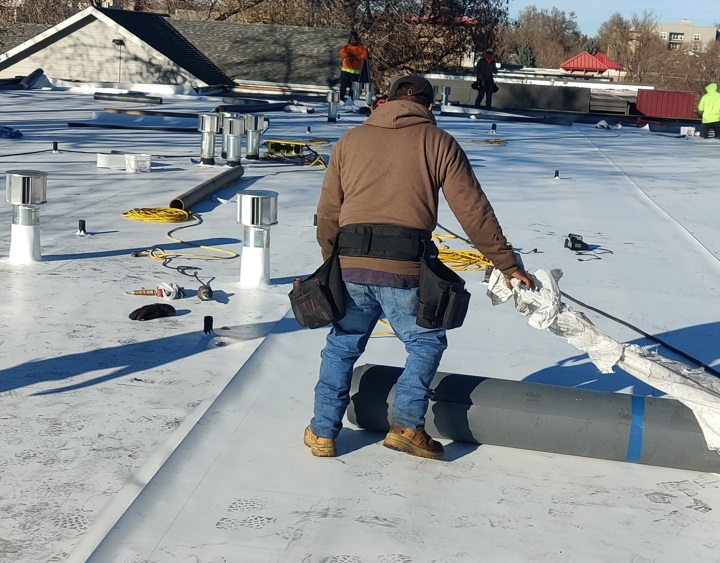
Durability and Longevity
When it comes to elastomeric roof coatings, their incredible durability and longevity are what truly set them apart. These liquid-applied membranes cure into an exponentially thicker, reinforced layer compared to traditional paints and coatings. The elastomeric formulation remains completely stable and unaffected by harsh UV radiation, extreme temperatures, wind, hail and the punishing freeze-thaw cycles we face here in Denver. It doesn’t chalk, peel or degrade over time like lesser roof coatings.
The elastomeric base also demonstrates superior elasticity to stretch and recover its shape, accommodating roof movement and preventing tears or ruptures. When properly applied over a sound, prepared substrate, these robust coatings can easily provide 10-15 years of waterproof protection, conservatively. Many of my commercial clients have even gotten 20+ years of service life from a quality elastomeric roof restoration before requiring a recoat or replacement. With their proven ability to withstand our extreme climate exposures, elastomeric coatings deliver incredible longevity and the lowest life-cycle costs.
Waterproofing
When these liquid applied membranes cure, they form an exponentially thicker, seamless, highly elastic barrier that is truly impermeable to water infiltration. The elastomeric formulation allows the coating to chemically bind directly to the roof substrate, eliminating any potential for moisture undertravel or leaks unlike coatings that simply topcoat the surface. Elastomerics also demonstrate incredible resistance to ponding water conditions that can lead to degradation and failure of other roofing systems over time.
Their unparalleled elasticity allows the coating to actually stretch and conform to changing water levels and movement without becoming dislodged or losing adhesion. Even under prolonged ponding, elastomeric membranes remain fully watertight and reinforced. When dealing with our heavy precipitation, snowfall and drainage issues, this resistance to ponding is crucial to preventing interior leaks and damage year after year. A high-quality elastomeric roof restoration essentially renews the weatherproof protection to provide decades of leak-free performance.
Cost-Effectiveness
One of the biggest selling points is the excellent cost-effectiveness of elastomeric roof coatings over the long run. Compared to the major expense of completely removing and replacing an aging roof system, an elastomeric restoration provides massive upfront savings at a fraction of the cost. There’s no tear-off, no disposal fees, and the installation process is incredibly fast with little disruption to operations. But the savings don’t stop there. With their incredible longevity and seamless, reinforced construction, elastomeric coatings require very little maintenance once applied besides periodic cleaning and inspections. This avoids costly leaks, repairs and premature replacements that really nickel-and-dime roofing budgets over time.
Many elastomeric formulations also have reflective cool roof properties to lower energy costs for air conditioning by reducing heat absorption. For building owners and property managers, those energy savings compound significantly over 15-20 years. When you factor in the low lifecycle costs and lack of disruption, an elastomeric roof restoration provides maximum return on investment for your rooftop.
Energy Efficiency
Elastomeric roof coatings can be an outstanding solution for commercial clients looking to reduce their utility costs. Many elastomeric formulations are designed as highly reflective ‘cool roof’ systems that reflect up to 85% of solar radiation to minimize heat absorption through the rooftop. This impressive reflectivity not only stems from the bright white color but also the UV-resistant chemistry that prevents discoloration and degradation over time from Denver’s intense high altitude sunlight.
While traditional coatings can become discolored and heat-absorbing as they age, elastomerics retain their heat-reflective properties and cooling capabilities for well over a decade of service life. By drastically reducing heat gain and thermal transfer, these reflective elastomeric membranes can lower air conditioning demands by up to 25% annually compared to darker roofing systems. This translates into significant long-term reductions in energy usage and operating costs while also decreasing their overall carbon footprint season after season. It’s an investment in protecting both their bottom line and the environment.
Environmental Benefits
Looking to ‘go green’ and reduce your environmental impact? Elastomeric roof coatings provide some excellent sustainable advantages. From a health standpoint, they are extremely low in VOCs and other toxic chemicals, so installation poses minimal indoor air quality concerns compared to solvent-based products. On the environmental front, elastomeric membranes are water-based, inorganic materials that don’t release greenhouse gases or pollutants during their long service life on the roof. Their exceptional longevity of 15-20 years also minimizes resource consumption, waste, and the carbon footprint associated with frequent roof replacements.
Many elastomeric formulations additionally provide ecological benefits by utilizing reflective ‘cool roof’ technology to reduce energy usage and associated emissions from power generation. For building owners truly committed to environmentally-conscious practices, an elastomeric roof restoration is an outstanding sustainable solution that limits exposure risks, diverts landfill waste, boosts energy efficiency and provides elite waterproof protection – all while avoiding the disruption of complete roof tear-off.
Components and Properties of Elastomeric Roof Coating
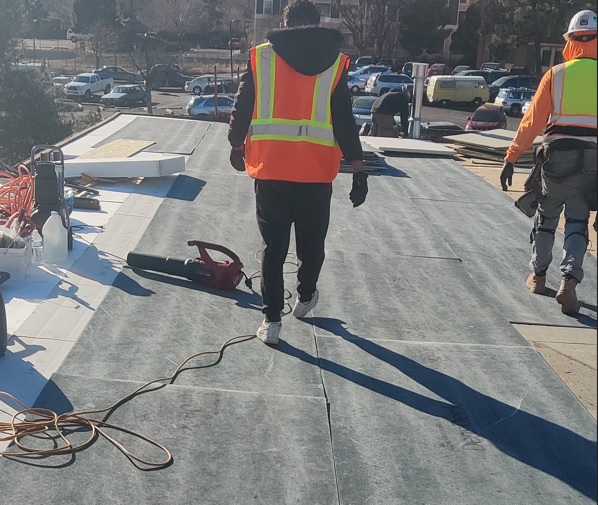
Material Composition
When you take a look closely at elastomeric roof coatings, you’ll find their chemical makeup varies quite a bit based on the specific elastomeric polymer used as the binding agent. The most common varieties are acrylic, silicone and urethane elastomerics. Acrylic formulations use a water based acrylic resin that provides excellent UV resistance, reflectivity, and breathability, making them a good cool roof solution. Silicone elastomerics employ high molecular weight silicone polymers and deliver superior weather, moisture, and ponding water resistance with incredible flexibility. Urethane-based elastomeric coatings start with a urethane rubber compound that creates a robust, abrasion-resistant membrane with outstanding tensile strength.
Beyond just the elastomeric binders, these coatings also incorporate mineral reinforcing compounds, specialty additives, and interlayers of fabric or polyester reinforcements when needed. This enhances their elongation capabilities, tear resistance, and ability to bridge hairline cracks. Selecting the right elastomeric formulation based on their facility’s needs allows us to maximize performance and longevity. Acrylic for cooler low-slope roofs, silicone for harsh exposures and ponding areas, and urethanes for high-traffic environments requiring ultimate durability.
Physical Properties
The physical properties of these elastomeric roof coatings are really what allows them to provide such exceptional waterproof performance and longevity. Their seamless liquid-applied nature eliminates any lap seams or joints that could allow moisture infiltration. But beyond just being monolithic, elastomerics demonstrate incredible elasticity and elongation – they can stretch up to 300% and then recover back to their original shape without rupturing. This flexibility prevents cracking and allows the membrane to conform to roof movements from thermal swings and structural shifts.
Elastomerics also chemically bonding directly to the roof substrate creating a fully reinforced system impervious to undertravel or delamination. We apply them at much greater thickness than conventional roof coatings – building up 30-60 dry mils to form an exponentially thicker, more robust waterproof barrier. When dealing with Denver’s punishing climate extremes, these superior physical properties provide a leak-free, worry-free roofing solution that protect your assets for decades.
Application Process
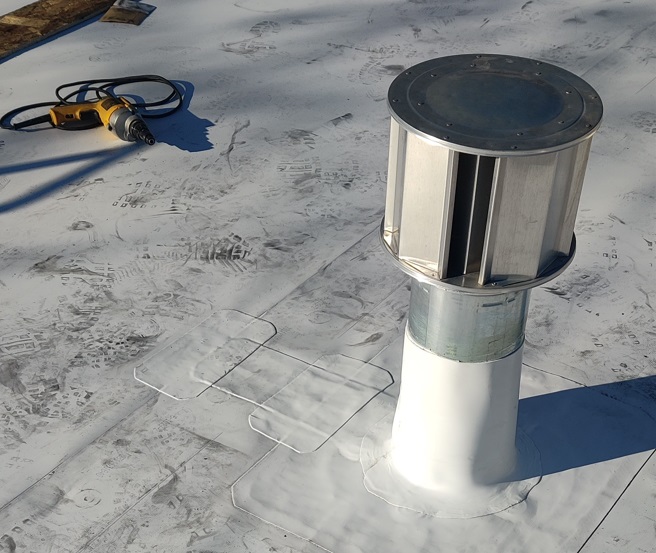
Preparation
Proper preparation of the existing roof surface is absolutely critical before my crews can install a long-lasting, effective elastomeric coating membrane. It ensures we have a sound, stable substrate that will maximize adhesion and allow the coating to perform optimally over its full service life. We start with a thorough roof inspection, carefully examining every inch to identify any areas of deterioration, damage or potential future issues that need to be addressed. This often involves removing loose gravel, debris, abandoned equipment or other materials that could puncture the new coating. We then make all necessary repairs – patching blisters, cracks and holes, re-securing flashings, replacing any wet insulation or deteriorated decking using compatible compounds.
Proper cleaning is also essential to remove dirt, grease, mildew or other contaminants that could inhibit full adhesion. Depending on the existing roof system, this may require pressure washing, chemical cleaners or priming. While this crucial prep work adds some time upfront, it’s an extremely wise investment. Going through these preparation steps ensures the elastomeric coating has a completely clean, intact surface to chemically bind to for a fully reinforced waterproof seal.
Application Methods
My team utilizes two primary techniques that we recommend based on the specific project scenario. For larger open roof areas with minimal obstructions or penetrations, we often employ an efficient spray application using specialized equipment and experienced technicians. This allows us to rapidly build up the required dry mil thickness of elastomeric coating across extensive surfaces for maximum productivity. The spray application fully encapsulates flashings and detail areas to create that monolithic, watertight surface.
For roofs with tighter spaces, more units, or interlocking designs, we’ll typically specify a roller application using high-quality woven nap rollers. Though more labor-intensive than spraying, this method enables us to properly saturate and coat all flashings, walls, and penetrations, ensuring no voids or pinholes in the elastomeric membrane. Whichever technique, we carefully monitor and ensure a final cured coating thickness of 30-60 dry mils depending on the specific elastomeric formulation and substrate. This exponentially thick, reinforced application is what gives the coating its incredible flexibility and robustness to bridge cracks and protect the roof’s watertight integrity for decades.
Curing Time
These products go through a chemical crosslinking as they cure to create that seamless, flexible membrane. Curing time can vary substantially based on factors like ambient temperature, humidity, and thickness of application. In ideal warm, dry conditions elastomeric coatings will typically achieve an initial set within 30 minutes to an hour. However, full cure to maximum chemical resistance and adhesion takes longer – typically 24-48 hours in the summer months when temperatures facilitate that curing process. Once fully cured, the coating has achieved its intended elastomeric properties. Lower temperatures and increased humidity can slow that cure rate considerably, so we plan application timing carefully during cooler months. My team also takes great care with thickness control during application to ensure the specified dry mil coverage. Too thick or uneven application can drastically impact cure time and long-term performance.