EPDM Roofing
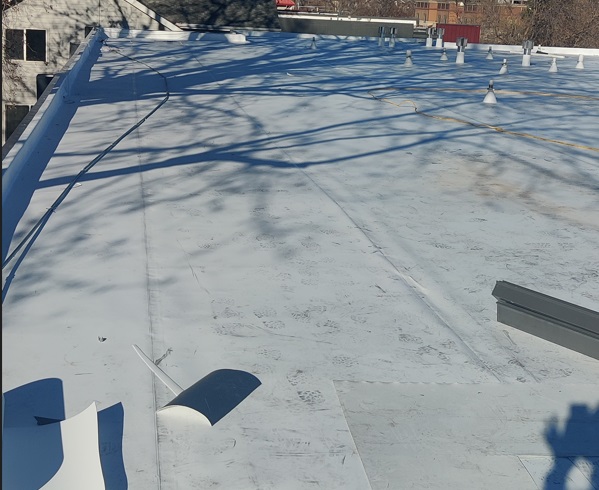
What is EPDM Roofing?
EPDM has become one of the most popular flat roofing systems for businesses and industrial facilities. EPDM, which stands for ethylene propylene diene monomer, is a versatile synthetic rubber roofing membrane that has become the go-to choice for its perfect blend of durability, weathering ability and cost-effectiveness.
Its low maintenance requirements are a major plus for busy facility managers and owners. Simply put, EPDM roofing is a smart long-term investment for Denver’s commercial properties.
resilient & Flexible
This extremely resilient material can easily withstand our harsh Rocky Mountain climate with its intense sun, hail storms, freeze-thaw cycles and heavy snow loads. EPDM’s flexibility makes it very resistant to thermal shock and leaks from building movement.
affordable & Reliable
It’s also one of the most affordable commercial roofing options while still providing excellence performance for 20-30 years with proper care. Whether for new construction or reroof projects, EPDM delivers reliable waterproof protection that keeps my clients’ buildings, equipment and operations running smoothly year after year.
Advantages of EPDM Roofing
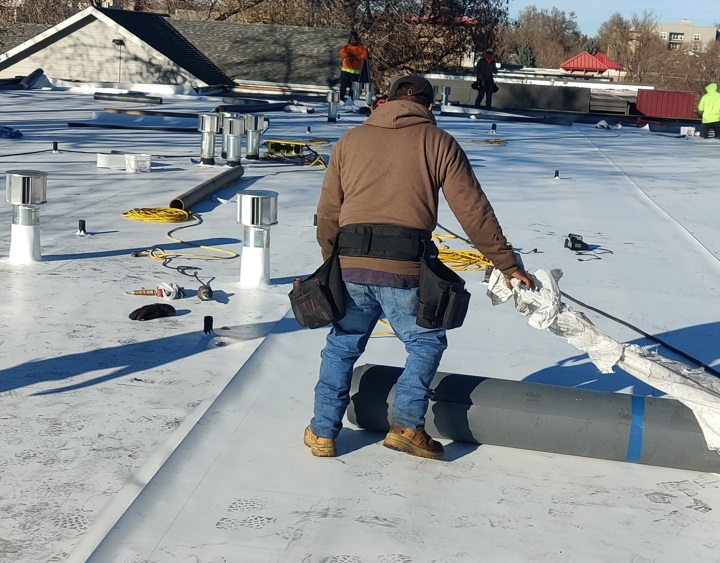
Durability and Longevity
When it comes to getting the most bang for your buck, EPDM’s durability and longevity are tough to beat. This synthetic rubber membrane is designed to withstand the harshest elements Mother Nature can dish out here in Denver. EPDM has superior resistance to UV radiation, wind, hail, snow loads and our constant freeze-thaw cycles without becoming brittle or cracking over time. Its flexibility allows it to expand and contract with temperature swings, preventing leaks from thermal shock. EPDM also has excellent ozone and weathering resistance to prevent breakdown from exposure.
Properly installed and maintained, an EPDM roof can easily last 25-30 years, with many examples even exceeding 35-40 year lifespans. That’s two to three times longer than cheaper modified bitumen or built-up roofing systems that require costly replacements every 10-15 years. For my Denver commercial clients, investing in an EPDM roof provides decades of waterproof protection and superior value compared to shorter-lived alternatives. It’s that combination of ruggedness and longevity that makes EPDM such a wise choice in our climate.
Waterproofing
Waterproofing is where EPDM really shines as far as I’m concerned. This synthetic rubber membrane forms an impermeable, monolithic surface that is virtually leakproof when installed correctly. Unlike modified bitumen and other multi-ply systems that have lap seams prone to failing over time, EPDM’s seams are sealed using a special tape that cures into a solid, rubberized bond just as waterproof as the membrane itself. This continuous barrier has no entry points for moisture infiltration.
EPDM also excels in situations with prolonged ponding water, which can be a major issue here after our heavy snowmelts or intense rainstorms. While standing water can potentially compromise other roofing materials by causing leaks or degradation, EPDM maintains its waterproof integrity. The membrane’s elasticity allows it to essentially float on the water without absorbing moisture or losing adhesion. This level of watertight protection gives building owners confidence that their roof can handle our precipitation extremes without costly interior damage.
Cost-Effectiveness
One of the biggest selling points for EPDM that I emphasize to my Denver commercial clients is its excellent cost-effectiveness over the long run. While the initial investment for an EPDM roof is higher than some basic roofing options, the pricing is very competitive with other premium single-ply systems like PVC or TPO. But where EPDM really pays off is through the long-term savings it provides. With its incredible longevity of 25-30 years, EPDM requires much less maintenance, repair, and replacement costs compared to roofs that need to be torn off every 10-15 years. Easy maintenance like regular cleaning and seam checks are all it takes to maximize EPDM’s lifespan. Its black reflective surface also helps reduce cooling energy usage.
When you factor in avoiding disruptive, expensive re-roofing projects every decade, EPDM has an extremely low life-cycle cost. For building owners and facility managers watching their bottom line, EPDM allows them to get top-tier waterproof performance and decades of hassle-free service at an affordable price point.
Energy Efficiency
When it comes to energy efficiency, EPDM provides an interesting dynamic with both reflective and absorptive properties. In its initial light-colored state, new EPDM has decent reflectivity to minimize heat absorption and reduce cooling costs. However, as the roof membrane naturally weathers and cycles through heat and UV exposure, it transforms to a darker charcoal color. This darker surface actually becomes more effective at absorbing solar heat in our cooler Denver climate during winter months.
By absorbing that low-angle winter sunlight, EPDM helps warm the building interior and cut down on heating demands. So the roofing essentially provides energy-saving benefits year-round by reducing both cooling and heating loads. This unique temperature-moderating effect from EPDM translates to lower overall HVAC costs and a smaller carbon footprint. When combined with the membrane’s exceptional insulating value and air-tightness, an EPDM roof can make a noticeable impact on decreasing energy usage and operating expenses over its very long lifespan.
Environmental Benefits
For commercial clients looking to ‘go green’ with an environmentally-friendly roofing option, EPDM checks off a lot of important boxes. Throughout its entire life cycle, EPDM has a relatively low environmental impact compared to other roofing systems. Its primary ingredients are synthetic rubber and recycled materials, without any harsh chemical components. The manufacturing process is also quite clean and efficient. Once installed on the roof, EPDM is an inert product that doesn’t release pollutants or toxins over its very long lifespan. This extreme durability reduces the need for frequent replacements and additional resource consumption.
When an EPDM roof finally does reach the end of its service life after 30-40 years, the membrane can be 100% recycled into new rubber products like playground surfaces and walkway materials. This recycling potential allows the old roof to avoid becoming waste in overflowing landfills. If you are committed to sustainability, EPDM provides high-performance waterproofing protection while minimizing their carbon footprint.
Components and Properties of EPDM Roofing
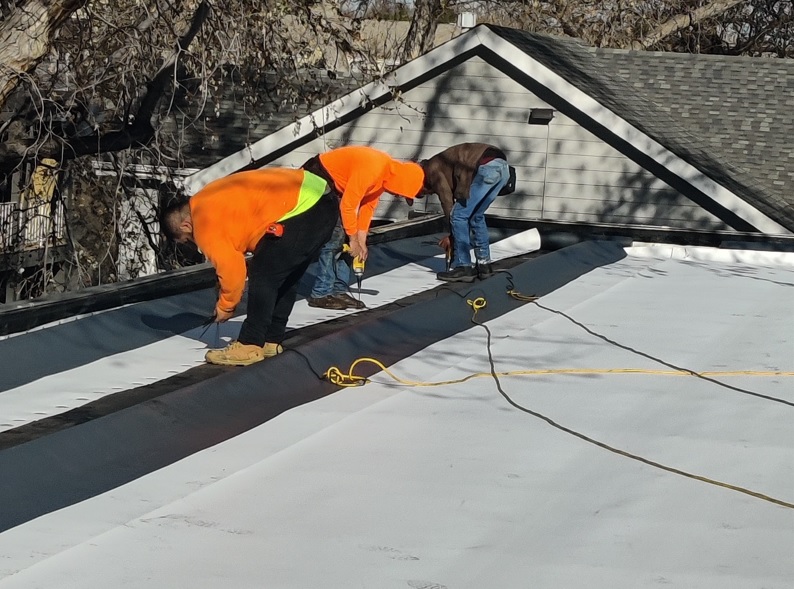
Material Composition
When you take a look under the hood at EPDM’s material makeup, you’ll find it’s quite unique compared to traditional low-slope commercial roofing systems. EPDM is a preformed synthetic rubber membrane derived primarily from ethylene and propylene along with some proprietary additives and curing agents to enhance weathering resistance. This rubber polymer composition is what gives EPDM its excellent flexibility, durability and ability to withstand thermal shock from temperature swings. Unlike modified bitumen or built-up roofing that utilizes asphalt, EPDM has no risk of drying out or becoming brittle with age.
It’s also monolithic and seamless when the sheets are properly seamed together using specialty tapes, avoiding the failure points of multi-ply systems. The cured rubber membrane is also highly resistant to ozone, oxidation, and UV radiation that can degrade other roofing over time. This durable synthetic composition allows EPDM to far outlast conventional asphalt-based roofs while providing superior weatherproofing capabilities.
Physical Properties
The physical properties of EPDM roofing are really what allow it to perform so exceptionally well in our harsh Rocky Mountain climate here in Denver. This synthetic rubber membrane remains incredibly flexible across an extremely wide temperature range – it can stretch and recover its shape even down to -40°F without becoming stiff or cracking. This elasticity prevents thermal shock and leaks from the freeze-thaw cycles and hot/cold swings we experience.
EPDM also has superior ozone and UV resistance compared to other roofing materials. Ozone can cause rubbers and plastics to deteriorate prematurely, but not EPDM. Its specialized polymer composition allows it to withstand this oxidizing effect for decades. The same goes for Denver’s intense high altitude UV radiation that can break down and dry out many roof systems. With EPDM, the cured membrane exhibits excellent UV weathering characteristics to prevent premature aging. These robust physical properties translate into a roof that maintains its waterproof integrity and protective performance capabilities for 30 years or more despite our extreme climate exposures.
Installation Process
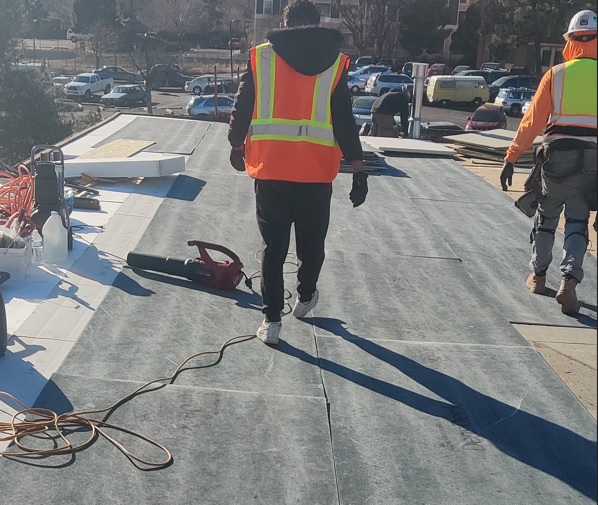
Preparation
Proper preparation is absolutely crucial before my crews can install a new EPDM roof membrane. It ensures we have a sound substrate that will maximize the roof’s service life and waterproofing performance. We start with a thorough inspection of the existing roof surface, carefully examining every inch for any defects, deterioration or areas of potential concern. This often involves removing debris, abandoned equipment or other materials that could cause punctures down the road. We then make any necessary repairs – patching blisters, sealing cracks, or fixing other minor damage using compatible products.
Proper cleaning is also essential to remove dirt, grease or other contaminants that could prevent proper adhesion of the new EPDM membrane. Depending on the existing assembly, this may involve power washing, chemical cleaning or scarifying the old surface. While this prep work adds some time upfront, it’s a critical investment. Going through these preparation steps guarantees the EPDM has a clean, stable surface to fully adhere to, preventing future leak issues right from the start.
Application Methods
When it comes to installing that durable EPDM membrane, my team has three primary techniques that we recommend based on the specific project requirements. For maximum wind uplift resistance on new construction projects, we often specify a fully adhered system where the EPDM sheets are bonded across the entire roof surface using a special adhesive. This ensures the roof stays firmly anchored during the high wind events we frequently experience here in Denver.
For re-roofing over an existing roof assembly, a mechanically attached system using rows of heavy-duty fasteners and barbed plates can be an effective option, especially on nailable wood decks. Both attachment methods create a sturdy, watertight roof system.
For renovations over a smooth existing surface like a metal roof, a ballasted EPDM application allows us to install the new membrane without excessive deck penetrations. We simply lay the EPDM sheets loose and weigh them down using concrete pavers along the perimeter and seams. Regardless of attachment method, all EPDM seams get sealed using specialty tapes that cure into a solid, monolithic bond just as watertight as the membrane itself. My team has expertise across all three installation styles to ensure your new EPDM roof is installed perfectly for optimum performance and longevity.
Timeframe
One of the top questions I get from commercial clients is ‘how long will this EPDM roof installation take?’ While every project is somewhat unique, I can provide a general timeframe. For a typical low-slope roof under 50,000 square feet with normal access, my experienced crews can usually get the entire EPDM installation process completed in 2-3 weeks from start to finish. This covers prepping the existing roof surface, laying out and seaming the new EPDM membrane, and all necessary flashing details. Larger roof areas or more complex designs with numerous penetrations will naturally extend that timeline a bit.
The attachment method can also be a factor – a fully adhered EPDM application may run slightly longer than a mechanically attached or ballasted system. Weather is always an X-factor too. Excessive precipitation or freezing temperatures can delay the EPDM installation until conditions improve. That’s why I recommend scheduling these projects during the drier, warmer periods if possible. Regardless of the timeline, my team is equipped to work efficiently while adhering to the highest standards of quality craftsmanship on every EPDM roof we install.