denver commercial roof coating – Silicone
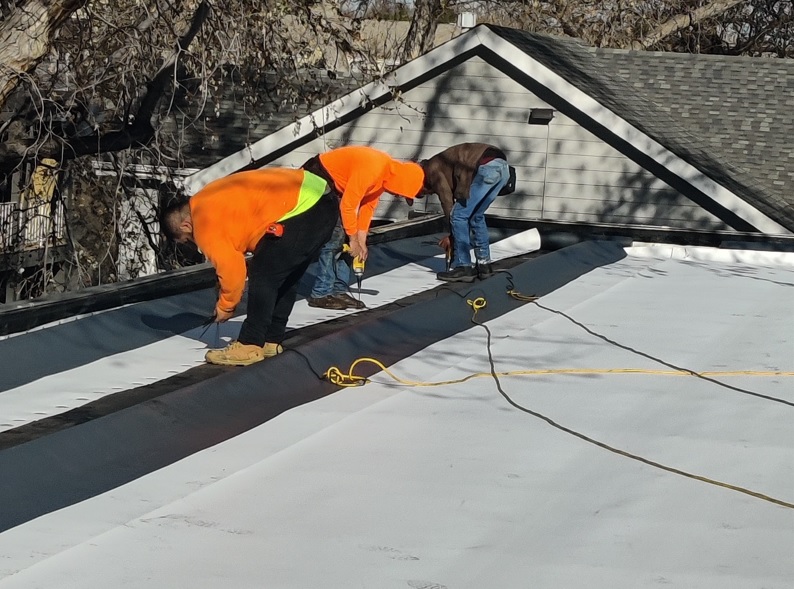
What is Silicone Roof Coating?
Silicone is essentially liquid applied roofing – a thick, rubber-like membrane that can be brushed, rolled or sprayed directly over an existing roof to form a seamless, waterproof barrier. This technology has been a game-changer, allowing us to cost-effectively restore and protect aging roof systems rather than replacing them entirely. Silicone coatings not only seal up leaks and extend the lifespan of the roof, but their highly reflective white surface also delivers huge energy savings by reducing cooling costs.
Maintenance & budget
Silicone is virtually hassle-free compared to traditional roofing. The coatings remain flexible to resist cracking, require no tear-offs, and can be easily refreshed with recoats over time. For commercial building owners dealing with limited budgets and operational disruptions, silicone provides a smart, sustainable solution to maximize their roofing investment while minimizing overhead expenses. It’s an essential tool in my arsenal for Denver’s unique climate demands.
Advantages of Silicone Roof Coating
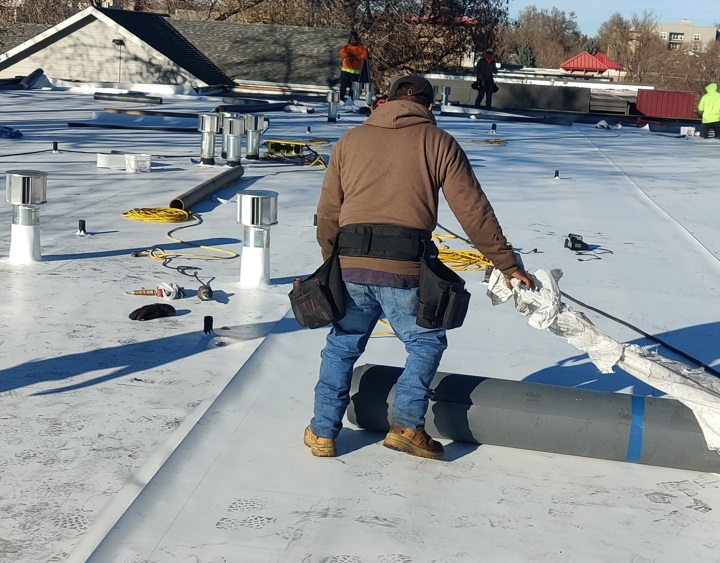
Durability and Longevity
When it comes to silicone roof coatings, their incredible durability and longevity are what really set them apart. This rubberized membrane forms an exponentially thicker, more resilient layer of protection compared to traditional paints and coatings. Silicone remains completely stable and unaffected by UV radiation, extreme temperatures, wind, rain, hail and the punishing freeze-thaw cycles we experience here in Denver. It doesn’t chalk, crack, peel or degrade over time like lesser coatings. Silicone also demonstrates superior flexibility to stretch and recover its shape, accommodating roof movement and preventing splits or ruptures.
When properly applied over a sound substrate, these coatings can provide waterproof protection for 10-15 years, conservatively. Many of my commercial clients have gotten 20+ years of service life from a quality silicone roof restoration. With relatively low-cost recoating every 10-15 years, that lifespan can be renewed and extended almost indefinitely. For building owners looking to get maximum value with low lifecycle costs, silicone delivers the rugged, lasting performance they need.
Waterproofing
Waterproofing is where silicone roof coatings really shine in my experience. When these liquid-applied membranes cure, they form an exponentially thicker, seamless, rubberized barrier that is truly impermeable to water. Silicone’s molecular composition allows it to chemically bind directly to the roof substrate, eliminating any risk of moisture undertravel or leaks. This watertight seal is far superior to roof coatings that simply topcoat the surface.
Silicone also excels at handling ponding water conditions that can lead to leaks and degradation with other roofing systems. Its unparalleled elasticity allows the membrane to actually stretch and conform to the changing water levels without losing adhesion or becoming dislodged. Even under prolonged ponding, silicone remains fully watertight. For my Denver commercial clients dealing with our heavy precipitation and snowmelt, this resistance to ponding water is crucial for preventing interior damage and avoiding costly hassles down the road. A high-quality silicone roof restoration provides truly leak-free, worry-free protection.
Cost-Effectiveness
One of the biggest selling points I emphasize is the excellent cost-effectiveness of silicone roof coatings over the long run. Compared to the expense of completely removing and replacing an aging roof system, a silicone restoration provides huge upfront savings – we’re talking a fraction of the cost. There’s no tear-off or disposal fees, and the installation process is incredibly quick and non-disruptive to your operations. But the savings don’t stop there. With silicone’s incredible longevity and renewable service life through simple recoating, you avoid those costly full roof replacements every 10-15 years like with traditional systems.
Maintenance is also a breeze, just an occasional cleaning and roof inspections. Maybe most significantly, that highly reflective white silicone surface helps reduce your cooling energy demands by up to 30% by minimizing heat absorption. For building owners and property managers, those energy cost reductions really add up over 15-20 years. When you factor in the low lifecycle costs and lack of disruption, silicone provides maximum return on investment for your rooftop.
Energy Efficiency
When it comes to energy efficiency, silicone roof coatings really can’t be beat. Their bright white surface has incredible reflective properties that drastically reduce heat absorption through the roof. By reflecting up to 85% of solar radiation, silicone acts as a highly effective “cool roof” that keeps temperatures inside the building far lower. This minimizes the demand on air conditioning systems, leading to serious energy cost savings – up to 30% in many cases. The reflective properties also stem from silicone’s extraordinary resistance to UV radiation breakdown and discoloration over time.
While other coatings and roofing membranes become discolored and heat-absorbing as they age, silicone retains its energy-efficient reflectivity and cooling capabilities for well over a decade. When dealing with our intense high altitude sunlight, this combination of reflectivity and UV stability is invaluable for controlling cooling costs and reducing their overall energy usage and carbon footprint season after season. It’s an investment that really pays dividends.
Environmental Benefits
If you are looking to ‘go green’ and reduce their environmental impact, silicone roof coatings check off all the key boxes. From a health standpoint, they are extremely low in VOCs and other toxic chemicals, so installation poses minimal indoor air quality concerns compared to solvent-based products. On the sustainability front, silicone membranes are inert, inorganic materials that don’t release greenhouse gases or pollutants over their long service life. Their exceptional longevity and renewability through recoating also minimizes resource consumption and waste compared to continual roof replacements.
Silicone’s reflective “cool roof” technology additionally provides ecological benefits by reducing energy usage and the associated carbon emissions from power generation. For building owners truly committed to environmentally-conscious practices, a silicone roof restoration is an outstanding solution that boosts energy efficiency, diverts landfill waste, and limits exposure risks – all while delivering elite waterproof protection. It’s a sustainable roofing approach that pays dividends for both your bottom line and the planet.
Components and Properties of Silicone Roof Coating
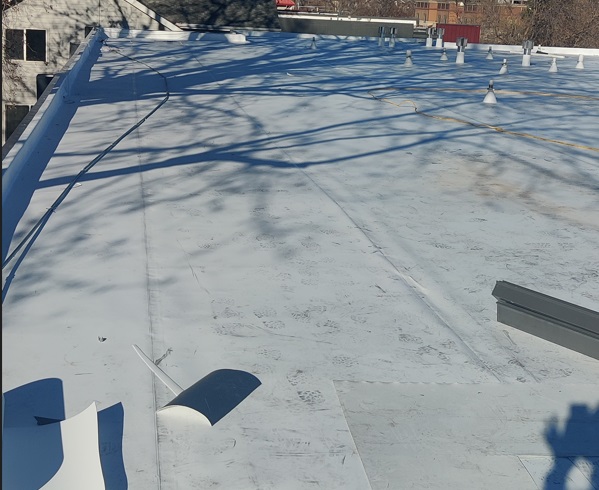
Chemical Composition
When you take a look under the hood at silicone roof coatings, you’ll find their chemical makeup is quite unique compared to traditional roof coatings and paints. The primary component is a high molecular weight silicone polymer blended with special siliconized acrylics and reinforcing compounds. This rubberized formula is what gives silicone its extraordinary elongation properties and superior flexibility compared to coatings that are essentially just thick paints. Unlike other acrylics that soften and re-emulsify when exposed to moisture and ponding water, silicone’s chemically cross-linked molecular structure allows it to retain dimensional stability and waterproofing integrity in all conditions.
The formulation is also thermoset rather than thermoplastic, meaning silicone won’t re-emulsify at high temps like some coatings can. This durable chemistry translates into a highly elastic, seamless membrane that bridges cracks, resists leaks, and provides exponentially longer service life. Silicone just outperforms and outlasts basic acrylic, urethane and aluminum products in every way.
Physical Properties
The physical properties of these silicone roof coatings are really what allow them to provide such exceptional weatherproof performance and energy efficiency. Right off the bat, their highly reflective bright white surface is incredibly effective at reflecting sunlight and UV radiation to minimize heat absorption. Silicone also has excellent emissivity to release any absorbed heat rather than transferring it into the building below. This natural “cool roof” technology translates into huge reductions in cooling costs for my commercial clients. But beyond just reflectivity, silicone stands apart with its extraordinary flexibility and elongation capabilities. The membrane can stretch and recover its shape up to 300% without rupturing to resist cracking and accommodate structural movements. This elastomeric flexibility prevents common modes of failure seen with rigid coatings.
Silicone also exhibits tenacious adhesion by chemically bonding directly to roof substrates to create a fully reinforced system impervious to moisture infiltration. In Denver’s harsh climate, these physical properties provide a truly robust, weathertight barrier that delivers maximum protection and energy savings over decades of service life.”
Application Process
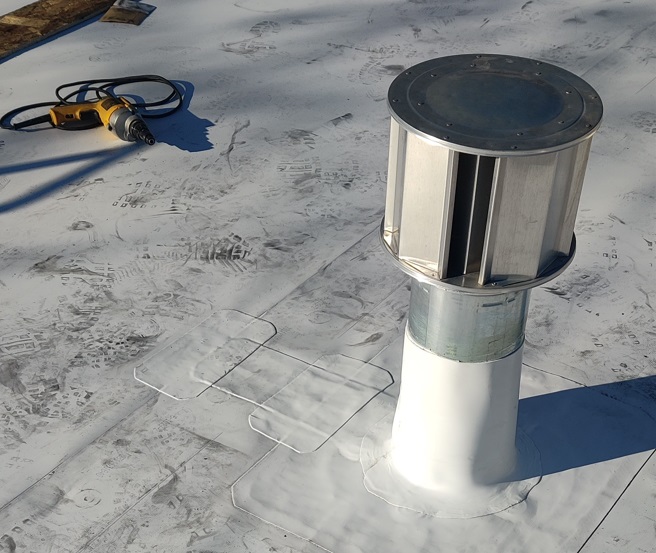
Preparation
Proper preparation of the existing roof surface is absolutely critical before my crews can install a long-lasting, effective silicone roof coating. It ensures we have a sound, stable substrate that will maximize adhesion and allow the silicone membrane to perform optimally. We start with a thorough roof inspection, carefully examining every inch to identify any areas of deterioration, damage or potential future issues. This often involves removing debris, abandoned equipment or other materials that could puncture the new coating. We then make any necessary repairs – patching blisters, sealing cracks and splits, fixing loose seams or flashing attachments using compatible sealants.
Proper cleaning is also essential to remove dirt, grease, mildew or other contaminants that could inhibit adhesion. Depending on the existing roof system, this may require pressure washing, chemical cleaners or priming. While this crucial prep work adds some time upfront, it’s an extremely wise investment. Going through these preparation steps ensures the silicone coating has a completely clean, intact surface to chemically bind to for a fully reinforced, waterproof seal.
Application Methods
My team utilizes two primary application techniques that we recommend based on the specific project scenario. For larger open roof areas with minimal obstructions or penetrations, we often employ an efficient spray application using specialized equipment and experienced technicians. This allows us to rapidly build up the desired dry mil thickness of silicone across extensive surfaces for maximum productivity. The spray application encapsulates flashings and seals while creating a smooth, monolithic coating.
For roofs with tighter spaces, more units, or interlocking designs, we’ll typically specify a roller application using high-quality woven nap rollers. This method ensures proper silicone thickness even in confined areas while allowing greater control and detailing around penetrations. Though more labor-intensive than spraying, the roller technique enables us to properly saturate all flashing reinforcements and seams for a impermeable, watertight seal across the entire roofing system. Whichever application style we use, my crews follow strict quality control measures to ensure every square foot receives the specified coverage without pinholes or holidays in the silicone coating.
Curing Time
Unlike some other roofing materials that can be walked on immediately, silicone needs adequate time to fully cure and form that seamless, reinforced membrane for maximum waterproofing and longevity. Under typical warm weather conditions here in Denver, we generally see an initial set time of 2-4 hours where the coating becomes tack-free. However, it requires 24-48 hours after application to achieve a complete cure and develop its full adhesion and strength properties. This curing duration can vary based on factors like temperature, humidity levels, air flow and coating thickness. Cooler temperatures or high humidity can significantly increase the cure time needed. That’s why we try to schedule silicone installations during the warmer seasons when possible. My teams also apply in multiple layers with recoats every 24 hours until the specified membrane thickness is built up. This maximizes interlayer adhesion for a truly monolithic coating once fully cured and cross-linked.