TPO (Thermoplastic Olefin) Roofing denver
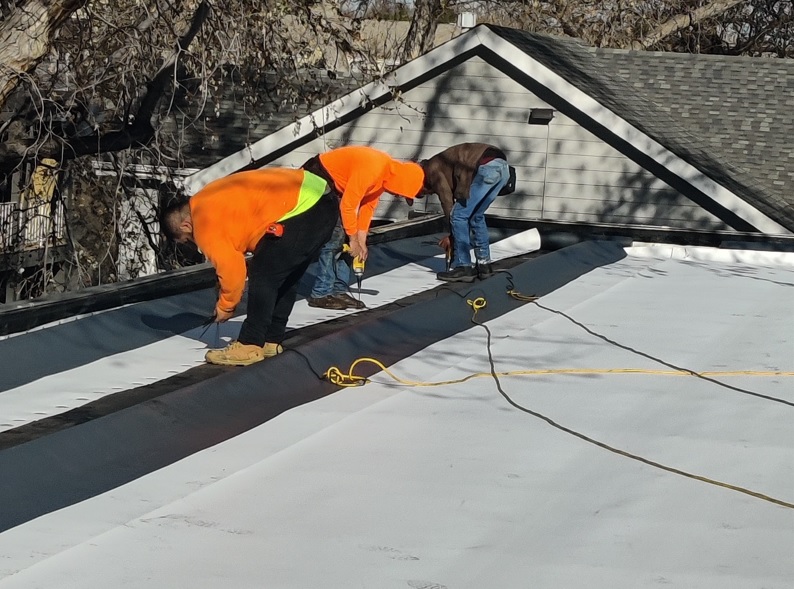
What is TPO Roofing?
TPO, which stands for Thermoplastic Polyolefin, is a single-ply roofing membrane that has gained significant popularity in recent years due to its many benefits and versatility.
TPO roofing was first introduced in the early 1990s as an alternative to other single-ply roofing systems like PVC and EPDM. Since then, it has undergone significant evolution and improvements, making it one of the most trusted and widely-used commercial roofing materials on the market today.
durability and performance
One of the key reasons for TPO’s growing importance in commercial roofing is its exceptional durability and long-term performance. TPO membranes are highly resistant to UV radiation, heat, and chemical exposure, which makes them an ideal choice for the harsh weather conditions we experience here in Denver. They also have excellent seam strength and puncture resistance, which helps to prevent leaks and ensure the longevity of the roofing system.
energy efficiency
Another significant advantage of TPO roofing is its energy efficiency. TPO membranes are available in white and other light colors, which can help to reflect sunlight and reduce heat absorption on the roof surface. This can translate to lower cooling costs for your building and improved overall energy efficiency.
versatility
In addition to its performance benefits, TPO roofing is also highly versatile and can be used on a wide range of commercial building types and styles. Whether you have a flat roof, a low-slope roof, or even a curved or irregular roof shape, TPO can be custom-fabricated to fit your specific needs and design requirements.
Consideration
If you’re considering a new roof for your commercial property here in Denver, I strongly encourage you to consider TPO as an option. My team and I would be happy to provide you with more information about the benefits of TPO roofing and help you determine if it’s the right choice for your specific needs and budget. With proper installation and maintenance, a TPO roof can provide decades of reliable protection and performance for your commercial building.
Advantages of TPO Roofing
One of the most significant advantages of TPO roofing that I always emphasize to my clients is its exceptional durability and longevity. When you invest in a TPO roofing system for your commercial property, you can have peace of mind knowing that you’re getting a product that is built to withstand the test of time and the elements.
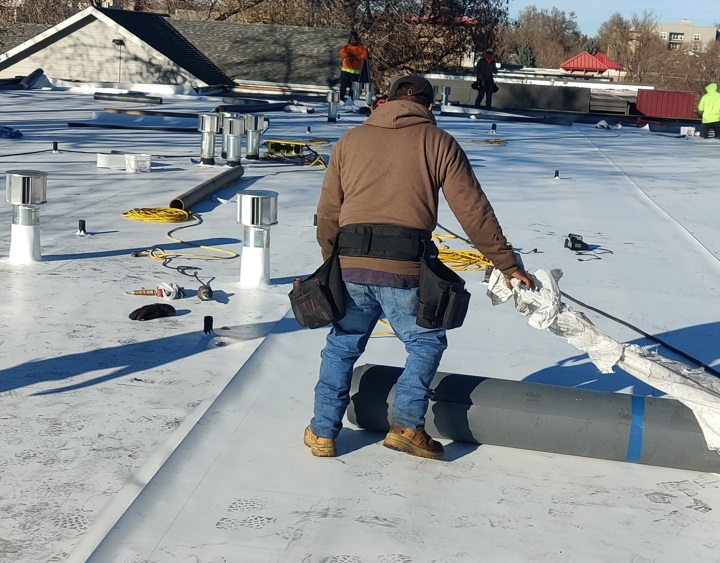
Durability and Longevity
TPO membranes are incredibly resilient and resistant to tears, punctures, and impact damage. This is due in large part to the unique composition of TPO, which includes a reinforcing scrim that provides added strength and stability to the membrane. Whether your roof is exposed to heavy foot traffic, hail storms, or other potential hazards, TPO is designed to maintain its integrity and performance over the long haul.
In fact, many manufacturers offer warranties on TPO roofing systems that extend up to 20 or even 30 years, which is a testament to the confidence they have in the durability and longevity of this product. As a roofing contractor, I’ve seen TPO roofs that look and perform like new even after 15 or 20 years of service, which is truly remarkable.
The actual lifespan of your TPO roof will depend on a variety of factors, including the quality of the installation, the level of maintenance and care it receives, and the specific environmental conditions it’s exposed to. That’s why it’s so important to work with an experienced and reputable roofing contractor who can ensure that your TPO roof is installed properly and in accordance with best practices and manufacturer guidelines.
We have a team of highly trained and certified TPO installers who have the knowledge and expertise to get the job done right. We use only the highest-quality TPO materials and adhere to strict installation protocols to ensure that every TPO roof we install is built to last.
When you choose TPO for your commercial roofing needs, you’re making a smart investment in the long-term protection and performance of your building. With its exceptional durability and longevity, TPO can help you avoid costly repairs and premature replacements down the line, while providing reliable, worry-free protection for your property and its occupants.
If you’re interested in learning more about the benefits of TPO roofing and how it can help extend the life of your commercial roof, I’d be happy to sit down with you and discuss your specific needs and goals. Together, we can develop a customized roofing solution that delivers the durability, longevity, and peace of mind you deserve.
Weather Resistance
I know how important it is to have a roofing system that can withstand the harsh weather conditions we experience in this region. That’s why I always make it a point to highlight the exceptional weather resistance of TPO roofing to my clients.
One of the biggest advantages of TPO is its ability to perform exceptionally well in extreme weather conditions. Whether you’re dealing with heavy snowfall, high winds, or intense UV radiation, TPO is designed to provide superior protection and durability.
Let’s start with TPO’s resistance to UV radiation and heat. As you may know, Denver is known for its high altitude and abundant sunshine, which can take a toll on many roofing materials over time. But TPO is specifically engineered to withstand prolonged exposure to UV rays and high temperatures without breaking down or deteriorating prematurely.
TPO membranes are often manufactured with advanced UV stabilizers and other additives that help to protect the material from the damaging effects of the sun. This not only helps to extend the lifespan of the roofing system but also helps to maintain its appearance and reflectivity over time, which can contribute to improved energy efficiency for your building.
But TPO’s weather resistance isn’t just limited to UV and heat protection. This material is also highly resistant to moisture, wind uplift, and extreme temperature fluctuations, making it an ideal choice for the variable weather conditions we experience here in Denver.
TPO’s heat-welded seams and secure attachment methods help to create a virtually impenetrable barrier against water infiltration, even in heavy rain or snowstorms. And its flexibility and elasticity allow it to expand and contract with temperature changes without cracking or splitting, which is crucial in a climate like ours where temperatures can vary widely from season to season.
I can say with confidence that this material has proven itself time and again in even the harshest weather conditions. I’ve seen TPO roofs emerge unscathed from hailstorms, blizzards, and high wind events that have caused significant damage to other types of roofing materials.
To fully realize the weather-resistant benefits of TPO, it’s important to choose a skilled and experienced installer who can ensure that the material is properly installed and detailed. We have a team of certified TPO installers who are trained in the latest best practices and quality control measures to ensure that every TPO roof we install is built to withstand the toughest weather challenges.
If you’re looking for a roofing system that can provide superior weather resistance and long-term performance in the demanding climate of Denver, I highly recommend considering TPO. With its exceptional UV and heat resistance, moisture and wind uplift protection, and overall durability, TPO is truly a top choice for commercial roofing in this region.
Cost-Effectiveness
I understand that cost is always a major consideration for building owners and managers when it comes to choosing a roofing system. That’s why I’m always excited to discuss the cost-effectiveness of TPO roofing with my clients.
One of the biggest advantages of TPO from a financial perspective is its competitive pricing. Compared to other high-performance single-ply roofing materials like PVC, TPO is often a more affordable option upfront. This is due in part to the lower cost of the raw materials used to manufacture TPO, as well as the efficiency of the production process.
But the cost-effectiveness of TPO goes beyond just the initial installation price. Over the long term, TPO can provide significant savings on energy and maintenance costs, making it an incredibly smart investment for building owners.
Let’s start with energy savings. As I mentioned earlier, TPO is available in white and other light colors that are highly reflective. This means that TPO can help to reflect solar radiation and heat away from your building, reducing the amount of heat that is absorbed into the interior space. This can translate to lower cooling costs and reduced strain on your HVAC system, especially during the hot summer months in Denver.
Many TPO roofing systems are ENERGY STAR® certified, which means they meet strict energy efficiency guidelines set by the U.S. Environmental Protection Agency. By installing an ENERGY STAR® certified TPO roof, you may be eligible for rebates and other incentives that can further offset the cost of installation.
But the savings don’t stop there. TPO is also known for its low maintenance requirements and long-term durability. Unlike some other roofing materials that may require frequent repairs or replacement due to wear and tear, TPO is designed to withstand the elements and maintain its performance for decades with minimal upkeep.
This means that you can avoid costly repairs and premature replacement, which can add up to significant savings over the life of your roof. And because TPO is so durable and resistant to common roofing problems like punctures, tears, and leaks, you can also minimize the risk of damage to your building’s interior and contents, which can be incredibly costly to repair. We’ve worked with building owners who have saved thousands of dollars on energy and maintenance costs over the years thanks to their TPO roofing system.
To fully realize the cost-saving benefits of TPO, it’s important to choose a reputable and experienced roofing contractor who can ensure that your roof is installed properly and in accordance with best practices. We use only the highest-quality TPO materials and adhere to strict installation standards to ensure that every TPO roof we install is built to perform and last.
If you’re looking for a roofing system that offers both competitive upfront pricing and long-term cost savings, I highly recommend considering TPO. With its energy efficiency, durability, and low maintenance requirements, TPO is truly a smart investment for any commercial building owner in Denver.
Energy Efficiency
I always make it a point to emphasize the exceptional energy efficiency benefits of TPO roofing to my clients. In a climate like ours, where we experience abundant sunshine and high temperatures during the summer months, having a roofing system that can help reduce energy costs and improve building comfort is a major advantage.
One of the key features of TPO that contributes to its energy efficiency is its reflective properties. TPO membranes are available in white and other light colors that have a high solar reflectance index (SRI). This means that they are designed to reflect a significant portion of the sun’s radiation back into the atmosphere, rather than absorbing it into the building.
By reflecting solar radiation TPO can help to reduce the amount of heat that enters your building through the roof. This can have a significant impact on your indoor temperatures and cooling costs, especially during the hot summer months. Studies have shown that a highly reflective TPO roof can reduce cooling costs by up to 30% compared to a non-reflective roof.
But the energy-saving benefits of TPO don’t stop there. Many TPO roofing systems are also designed with additional insulation layers that can help to further reduce heat transfer and improve the overall thermal performance of your building. This can be especially beneficial in the winter months, when you want to keep heat inside your building and reduce the burden on your heating system.
As a building owner, investing in an energy-efficient TPO roofing system can provide significant long-term cost savings and environmental benefits. By reducing your energy consumption and reliance on fossil fuels, you can lower your carbon footprint and contribute to a more sustainable future. We’ve worked with clients who have reported significant reductions in their cooling costs and improved indoor comfort levels after installing a TPO roof.
To fully realize the energy efficiency benefits of TPO, it’s important to choose a product with a high solar reflectance index and to work with a reputable installer who can ensure that the roof is properly insulated and detailed. We use only the highest-quality TPO materials and adhere to strict installation standards to maximize the energy performance of every roof we install.
We also offer energy performance assessments and can provide guidance on additional strategies for improving the energy efficiency of your building, such as adding skylights or upgrading your HVAC system.
In today’s world, where energy costs and environmental concerns are top of mind for many building owners, investing in an energy-efficient TPO roofing system just makes sense. Not only can it provide significant cost savings over the life of your roof, but it can also help to create a more comfortable and sustainable building environment for your occupants.
If you’re interested in learning more about how a TPO roofing system can improve the energy efficiency of your commercial building in Denver, I’d be happy to sit down with you and discuss your options. With the right product and installation, you can enjoy all the benefits of a high-performance, energy-efficient roof for years to come.
Environmental Benefits
In today’s world, where sustainability and eco-friendliness are becoming increasingly important considerations for building owners and managers, TPO stands out as a roofing material that can contribute to a greener built environment.
One of the most significant environmental benefits of TPO is its recyclability. Unlike some other roofing materials that end up in landfills at the end of their lifespan, TPO can be recycled and repurposed into new products. This is because TPO is a thermoplastic material that can be melted down and reformed without losing its physical properties.
Many TPO manufacturers have established recycling programs that allow contractors like myself to collect and return used TPO membranes for recycling. This not only helps to reduce waste and conserve resources but also supports the development of new, eco-friendly products made from recycled TPO.
In addition to its recyclability, TPO can also contribute to LEED (Leadership in Energy and Environmental Design) credits for building owners seeking to achieve green building certification. LEED is a widely recognized rating system that evaluates the environmental performance of buildings based on criteria such as energy efficiency, water conservation, and materials selection.
By installing a TPO roofing system with a high solar reflectance index (SRI), building owners can earn LEED credits in the Sustainable Sites and Energy and Atmosphere categories. This is because a reflective TPO roof can help to reduce the urban heat island effect, mitigate storm water runoff, and improve the energy efficiency of the building.
I encourage my clients to consider the long-term environmental impact of their roofing choices. By choosing a TPO roofing system building owners can not only enjoy the many performance benefits of this material but also contribute to a more sustainably built environment.
We are proud to offer TPO roofing systems from manufacturers who are committed to sustainability and environmental responsibility. We also follow best practices for recycling and waste reduction on all of our job sites, and we can provide guidance on additional strategies for improving the environmental performance of your building.
Whether you’re seeking to achieve LEED certification, reduce your carbon footprint, or simply make a positive impact on the environment, a TPO roofing system can be an excellent choice. With its recyclability, energy efficiency, and durability, TPO offers a win-win solution for building owners looking to balance performance and sustainability.
If you’re interested in learning more about the environmental benefits of TPO and how it can contribute to your building’s sustainability goals, I would be happy to discuss your options in more detail. As a trusted roofing advisor and sustainability advocate, I’m committed to helping my clients make informed decisions that are good for their buildings, their bottom line, and the planet.
Components of TPO Roofing
One of the most critical components of a TPO roof is the membrane itself, which is a single-ply layer that serves as the primary waterproofing and protective barrier for your building.
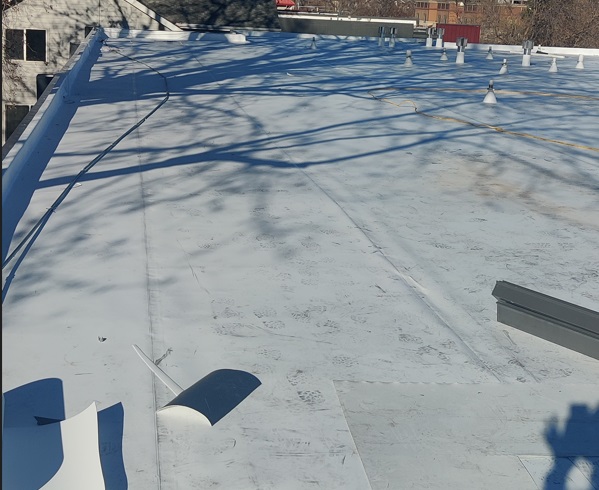
Membrane Layers
TPO membranes are typically manufactured in large rolls that are mechanically attached or adhered to the roof deck and then heat-welded together at the seams to create a seamless, monolithic surface. One of the great things about TPO is that it comes in a range of thickness options to suit different budgets and performance requirements.
The most common TPO membrane thicknesses are 45 mils, 60 mils, and 80 mils. A mil is a unit of measurement equal to one-thousandth of an inch, so a 60-mil TPO membrane, for example, would be 0.060 inches thick.
As a general rule, thicker TPO membranes offer greater durability, puncture resistance, and long-term weathering performance than thinner membranes. For example, an 80-mil TPO membrane can provide up to 33% greater puncture resistance and 47% greater break strength than a 45-mil membrane, making it an ideal choice for high-traffic areas or buildings with heavy rooftop equipment.
It’s important to note that even the thinnest TPO membranes on the market today are still highly durable and can provide excellent long-term performance when properly installed and maintained. In fact, many manufacturers offer similar warranties for their 45-mil and 60-mil membranes as they do for their 80-mil products.
We help my clients select the TPO membrane thickness that best balances their performance needs and budget. I take into account factors such as the building’s location, climate, and intended use, as well as the client’s long-term goals and expectations for their roof.
We only install TPO membranes from trusted manufacturers with proven track records of quality and performance. We also follow best practices for installation and quality control to ensure that every TPO membrane we install is properly secured, welded, and detailed for maximum durability and longevity.
Whether you choose a 45-mil, 60-mil, or 80-mil TPO membrane for your commercial roof in Denver, you can rest assured that you are getting a high-quality, high-performance product that is built to withstand the toughest weather conditions and provide long-term value for your building.
If you’re interested in learning more about the different TPO membrane thickness options and which one might be right for your specific needs and budget, I would be happy to sit down with you and discuss your options in more detail. With the right TPO membrane and installation, you can enjoy all the benefits of a durable, energy-efficient, and cost-effective roofing system for years to come.
Reinforcements
While the TPO membrane itself is the most visible component of the roof, there are other important elements that work behind the scenes to provide additional strength, stability, and durability. One of these critical components is the reinforcement layer.
TPO membranes are typically reinforced with either polyester or fiberglass to enhance their strength and dimensional stability. These reinforcements are embedded within the TPO polymer during the manufacturing process, creating a composite material that is stronger and more resilient than the TPO polymer alone.
Polyester reinforcements are the most common type used in TPO membranes today. Polyester is a strong, flexible, and affordable material that provides excellent tear resistance and long-term durability. It also has a high melting point, which helps to prevent shrinkage and maintain the membrane’s shape and size over time.
Fiberglass reinforcements are another option that some TPO manufacturers offer. Fiberglass is known for its high tensile strength and dimensional stability, which can help to prevent the TPO membrane from stretching or deforming under stress. It is also highly resistant to moisture and chemical exposure, making it a good choice for buildings with harsh environmental conditions.
The choice between polyester and fiberglass reinforcements will depend on the specific needs and priorities of your building and your budget. As a roofing contractor, I always work closely with my clients to understand their unique requirements and recommend the reinforcement option that will provide the best long-term value and performance for their specific situation.
Regardless of which reinforcement type you choose, it’s important to work with a reputable TPO manufacturer and a skilled installation team to ensure that the reinforcement layer is properly integrated with the TPO membrane and installed according to best practices. We only use high-quality TPO products from trusted manufacturers, and our installation crews are highly trained and experienced in working with both polyester and fiberglass reinforcements.
In addition to the reinforcement layer, there are other important components of a TPO roofing system that work together to provide a complete, high-performance solution. These include the insulation layer, the cover board, and the adhesives and fasteners used to secure the system to the roof deck.
Whether you’re interested in learning more about TPO reinforcements or any other aspect of the roofing process, I’m here to answer your questions and provide the expert guidance you need to make the right choice for your specific needs and budget. So if you’re considering a new TPO roof for your commercial building in Denver, I invite you to reach out to me and my team to schedule a consultation. We’ll take the time to understand your unique requirements and provide a customized recommendation that will help you achieve your goals and protect your investment for years to come.
Attachment Methods
One of the most important decisions we’ll make when designing your TPO roofing system is how to attach the membrane to your roof deck. The attachment method we choose will have a significant impact on the overall performance, durability, and cost of your roof, so it’s essential to understand the options available and select the one that best suits your specific needs and budget.
There are three primary attachment methods for TPO roofing systems: mechanically attached, fully adhered, and ballasted. Each method has its own unique advantages and disadvantages, and the right choice for your building will depend on a variety of factors, including your roof slope, deck type, and local wind and weather conditions.
Mechanically attached TPO systems are the most common and economical option. With this method, the TPO membrane is attached to the roof deck using a series of fasteners and plates that are spaced at regular intervals along the seams of the membrane. This creates a strong, secure attachment that can resist high winds and uplift forces. Mechanically attached systems are ideal for buildings with metal or wood decks and can be installed quickly and efficiently, making them a popular choice for many commercial projects.
Fully adhered TPO systems, on the other hand, involve bonding the entire underside of the TPO membrane to the roof deck or substrate using a special adhesive. This creates a seamless, monolithic surface that is highly resistant to wind uplift and moisture infiltration. Fully adhered systems are a good choice for buildings with concrete or gypsum decks, as well as those with irregular or complex roof shapes. They also provide excellent energy efficiency and can help to reduce noise transmission into the building.
Finally, ballasted TPO systems involve loose-laying the TPO membrane over the roof deck and then covering it with a layer of ballast, such as gravel or pavers. The weight of the ballast helps to hold the membrane in place and resist wind uplift forces. Ballasted systems are a good choice for large, low-slope roofs where mechanical attachment or full adhesion may not be practical or cost-effective. They also offer excellent puncture resistance and can help to extend the life of the TPO membrane.
We will help you select the TPO attachment method that will provide the best long-term value and performance for your specific building and budget. I’ll take into account factors such as your roof slope, deck type, and local wind speeds, as well as your energy efficiency and sustainability goals.
We have extensive experience installing all three types of TPO attachment methods, and we use only the highest-quality products and techniques to ensure a durable, long-lasting roof. Whether you choose a mechanically attached, fully adhered, or ballasted system, you can rest assured that your TPO roof will be installed to the highest standards of quality and craftsmanship.
If you’re considering a new TPO roof for your commercial building in Denver, I invite you to contact me and my team to schedule a consultation. We’ll work closely with you to understand your unique needs and provide a customized recommendation that will help you achieve your goals and protect your investment for years to come. With the right TPO attachment method and installation, you can enjoy all the benefits of a high-performance, energy-efficient roofing system that will provide lasting value and protection for your commercial property.
Installation Process
I cannot stress enough the importance of proper preparation before installing a new TPO roofing system. The success and longevity of your new roof depend heavily on the condition of your existing roof and the steps we take to prepare it for the new installation.
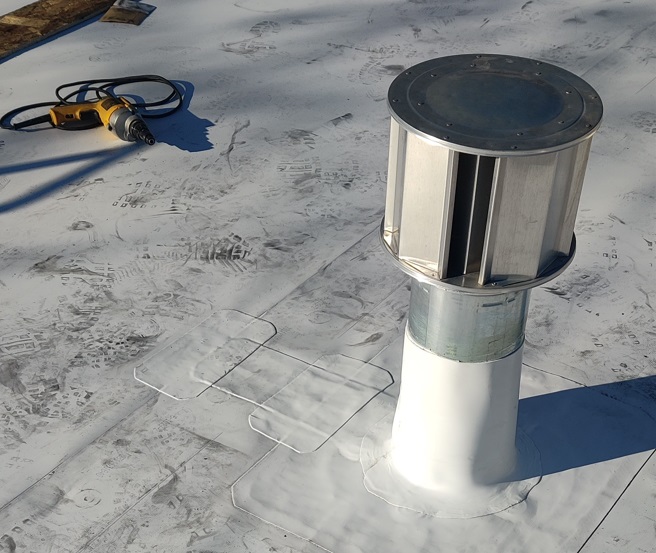
Preparation
The first step in any TPO installation project is a thorough inspection of your existing roof. This allows us to assess the overall condition of your roof deck, identify any areas of damage or deterioration, and determine if any repairs or upgrades are necessary before we begin installing the new TPO system.
During the inspection we’ll look for signs of water damage, such as rotting wood, rusted metal, or saturated insulation. We’ll also check for any areas of unevenness or instability in the roof deck that could compromise the performance of the new TPO membrane. If we identify any issues during the inspection, we’ll work with you to develop a plan to address them before moving forward with the installation.
Once we’ve completed the inspection and made any necessary repairs, we’ll move on to the surface cleaning and preparation phase. This is a critical step in ensuring that the new TPO membrane adheres properly to the roof deck and provides a seamless, watertight barrier.
We’ll start by thoroughly cleaning the roof surface to remove any dirt, debris, or contaminants that could interfere with the adhesion of the new TPO membrane. This may involve using power brooms, air blowers, or pressure washers, depending on the condition of the roof and the type of debris present.
Next, we’ll make sure that the roof surface is smooth, even, and free of any sharp edges or protrusions that could damage the TPO membrane over time. This may involve applying a layer of cover board or insulation to create a uniform surface, or making spot repairs to any areas of unevenness or damage.
Finally, we’ll apply a layer of primer or adhesive to the roof surface to help the new TPO membrane adhere properly and create a strong, long-lasting bond. The type of primer or adhesive we use will depend on the specific TPO product we’re installing and the conditions of your roof.
We are a team of experienced professionals who are trained in the latest TPO installation techniques and best practices. We use only the highest-quality materials and equipment to ensure that every TPO roof we install meets or exceeds the manufacturer’s specifications and provides optimal performance and durability.
By taking the time to properly inspect and prepare your existing roof before installing the new TPO system, we can help extend the life of your roof, minimize the risk of leaks and other issues, and ensure that your investment in a new TPO roof pays off in the long run.
If you’re considering a TPO roof for your commercial building in Denver, I encourage you to contact me and my team to schedule a consultation. We’ll work closely with you to assess the condition of your existing roof, recommend any necessary repairs or upgrades, and develop a customized installation plan that meets your specific needs and budget. With our expertise and attention to detail, you can trust that your new TPO roof will provide reliable, long-lasting protection for your commercial property.
Installation Methods
The right installation method for your TPO roofing system is a critical decision that can impact the performance, longevity, and cost of your new roof. There are three primary installation methods for TPO roofing systems: mechanically fastened, fully adhered, and ballasted. Each method has its own unique advantages and disadvantages, and the best choice for your building will depend on a variety of factors.
Let’s start with mechanically fastened TPO systems. This is the most common and cost-effective installation method, and it involves securing the TPO membrane to the roof deck using a series of fasteners and plates along the seams of the membrane. The fasteners are typically installed every 12 inches along the seams, creating a strong, secure attachment that can withstand high winds and uplift forces. Mechanically fastened systems are a great choice for buildings with metal or wood decks, as well as those with irregular or complex roof shapes. They are also the fastest and easiest TPO installation method, which can help reduce labor costs and minimize disruption to your business operations.
Fully adhered TPO systems, on the other hand, involve bonding the entire underside of the TPO membrane to the roof deck or substrate using a special adhesive. This creates a seamless, monolithic surface that is highly resistant to wind uplift and moisture infiltration. Fully adhered systems are ideal for buildings with concrete or gypsum decks, as well as those with high moisture or humidity levels. They also provide excellent energy efficiency and can help reduce noise transmission into the building. However, fully adhered systems are more labor-intensive and time-consuming to install than mechanically fastened systems, which can increase the overall cost of the project.
Finally, ballasted TPO systems involve loose-laying the TPO membrane over the roof deck and then covering it with a layer of ballast, such as gravel or pavers. The weight of the ballast helps to hold the membrane in place and resist wind uplift forces. Ballasted systems are a good choice for large, low-slope roofs where mechanical attachment or full adhesion may not be practical or cost-effective. They also offer excellent puncture resistance and can help extend the life of the TPO membrane. However, ballasted systems are not suitable for all building types and may not be permitted by local building codes in some areas.
Timeframe
One of the most common questions I receive from clients is how long it will take to install their new TPO roofing system. The answer to this question can vary depending on several factors, but in general, most TPO installations can be completed within a few weeks to a month, depending on the size and complexity of the project.
When estimating the timeline for a TPO installation, there are several key factors that I take into consideration. The first is the size of the roof. Larger roofs will naturally take longer to install than smaller roofs, simply because there is more surface area to cover and more materials to install.
Another important factor is the complexity of the roof design. Roofs with multiple levels, steep slopes, or numerous penetrations (such as skylights or HVAC units) will require more time and labor to install than simpler, flat roofs. This is because these complex areas require additional flashing, sealing, and detailing to ensure a watertight and durable installation.
The weather can also play a significant role in the installation timeline. While TPO can be installed year-round, extreme temperatures, high winds, or heavy precipitation can delay or slow down the installation process. In Denver, we can experience a wide range of weather conditions throughout the year, so it’s important to factor in potential weather delays when estimating the project timeline.
Other factors that can impact the installation timeline include the availability of materials and labor, the condition of the existing roof deck, and any unforeseen issues that may arise during the installation process. We use a proven installation process that is designed to maximize efficiency and minimize disruption to your business operations.
Before we begin any TPO installation project, we’ll work with you to develop a detailed project plan and timeline that takes into account all of the factors mentioned above. We’ll also provide you with regular updates throughout the installation process, so you always know what to expect and when to expect it.
In general, a typical TPO installation timeline might look something like this:
- Week 1: Inspection and preparation of the existing roof deck, including any necessary repairs or upgrades.
- Week 2-3: Installation of the TPO membrane, flashing, and other components, depending on the size and complexity of the roof.
- Week 4: Final inspection, cleanup, and walkthrough with the client to ensure satisfaction and address any concerns.
Of course, this is just a general timeline, and the actual duration of your TPO installation project may vary depending on your specific needs and circumstances. With our expertise and attention to detail, you can trust that your new TPO roof will be installed efficiently, effectively, and with minimal disruption to your business operations.
TPO Roofing in Denver, Colorado
Denver is known for its extreme temperature fluctuations, with cold, snowy winters and hot, sunny summers. This can put a lot of stress on a roofing system, so it’s essential to choose a material that can withstand these conditions and provide reliable, long-lasting protection for your building.
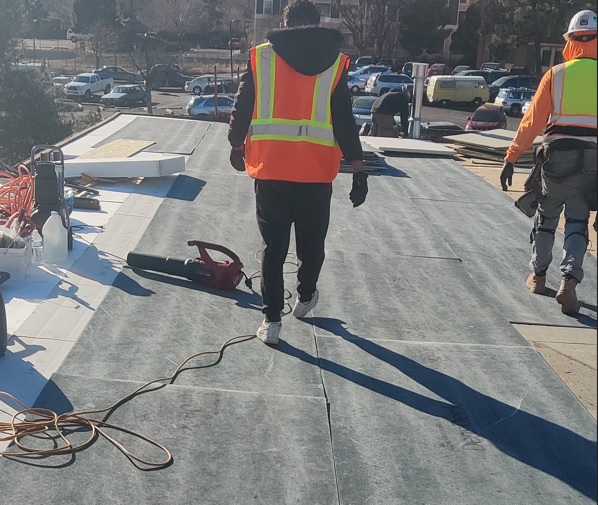
Climate Adaptability
I often recommend TPO roofing systems to my clients in Denver. TPO is a highly adaptable and resilient material that is designed to perform well in a wide range of climates, including the harsh conditions we experience here in the Mile High City.
During our cold winters, TPO remains flexible and resistant to cracking or shattering, even in sub-zero temperatures. This is because TPO is made with a special blend of rubbers and polymers that remain pliable and elastic in cold weather, allowing the membrane to expand and contract with temperature changes without breaking or losing its seal.
In the summer months, TPO’s reflective properties help to keep your building cool and reduce your energy costs. TPO membranes are available in white and other light colors that reflect up to 85% of the sun’s rays, helping to reduce heat absorption and keep your building’s interior comfortable and cool. This can be especially beneficial in Denver, where we have over 300 days of sunshine per year and temperatures that can soar into the 90s and 100s.
Another advantage of TPO in Denver’s climate is its exceptional resistance to UV radiation. Our high altitude and intense sunlight can cause some roofing materials to break down and deteriorate over time, leading to leaks and other issues. But TPO is specifically engineered to withstand prolonged exposure to UV rays, with advanced stabilizers and anti-oxidants that help prevent cracking, fading, and other signs of aging.
We use only the highest-quality TPO membranes from trusted manufacturers, and our installation teams are trained in the latest techniques and best practices for ensuring a durable, long-lasting installation.
When we install a TPO roof on your building, we take into account all of the unique factors that can impact its performance, including your building’s location, orientation, and surrounding environment. We also use specialized equipment and techniques to ensure that the TPO membrane is properly sealed and secured to your roof deck, with no gaps or weak spots that could allow water or air infiltration.
If you’re considering a new roofing system for your commercial building in Denver, I highly recommend considering TPO. With its proven track record of performance in our challenging climate, TPO can provide your building with reliable, long-lasting protection against the elements, while also helping to reduce your energy costs and maintain a comfortable indoor environment.
Local Building Codes and Regulation
Denver has strict standards in place to ensure the safety, durability, and energy efficiency of commercial buildings, and it’s essential to choose a roofing system that meets or exceeds these requirements.
When it comes to TPO roofing, I’m happy to say that this material is fully compliant with all current Denver building codes and regulations. In fact, TPO has become increasingly popular in Denver in recent years, thanks in part to its ability to meet the city’s stringent energy efficiency and sustainability standards.
One of the key requirements for commercial roofing in Denver is that the roofing material must have a minimum slope of 1/4 inch per foot to ensure proper drainage and prevent ponding water. TPO is well-suited to meet this requirement, as it can be installed on roofs with slopes as low as 1/4 inch per foot, without the need for additional tapered insulation or crickets.
Another important consideration is the fire rating of the roofing material. Denver requires all commercial roofing systems to have a Class A fire rating, which is the highest rating available. TPO meets this requirement, with fire ratings that exceed the minimum standards set by the city.
In addition to these basic requirements, Denver also has specific regulations related to energy efficiency and sustainability. The city has adopted the 2015 International Energy Conservation Code (IECC), which sets minimum standards for insulation, air sealing, and other energy-efficient features in commercial buildings.
TPO is an excellent choice for meeting these energy efficiency standards, thanks to its reflective properties and ability to reduce heat absorption on the roof surface. By installing a TPO roof with a high Solar Reflectance Index (SRI), you can help reduce your building’s cooling costs and contribute to Denver’s goals of reducing energy consumption and greenhouse gas emissions.
Before we begin any TPO roofing project, we conduct a thorough assessment of your building and its specific requirements, to ensure that we are using materials and installation methods that meet or exceed all applicable standards.
We also work closely with city inspectors and other officials to ensure that our work is fully compliant and up to code. This includes obtaining all necessary permits and approvals, and scheduling inspections at key milestones throughout the project to verify that our work meets the city’s standards. We pride ourselves on our commitment to quality, safety, and compliance, and we go above and beyond to ensure that every TPO roof we install meets the highest standards of performance and durability. With our expertise and dedication to quality, you can trust that your new TPO roof will provide you with years of reliable, energy-efficient protection for your commercial building.
Environmental Factors
Environmental factors can impact the performance and longevity of any roofing system. Here in Denver, we have some specific considerations that need to be taken into account when selecting a roofing material, particularly when it comes to energy efficiency and UV resistance at high altitudes.
At an elevation of over 5,000 feet above sea level, Denver’s high altitude presents both challenges and opportunities when it comes to roofing. The thinner air and increased solar radiation at high altitudes can lead to higher levels of UV exposure and heat gain on the roof surface. This can cause some roofing materials to break down and deteriorate more quickly, leading to reduced performance and lifespan.
TPO roofing is particularly well-suited to meet these challenges, thanks to its exceptional UV resistance and energy efficiency properties. TPO membranes are engineered with advanced UV stabilizers and anti-oxidants that help prevent cracking, fading, and other signs of aging caused by prolonged exposure to sunlight. This means that a TPO roof installed in Denver can maintain its appearance and performance for many years, even under the intense UV radiation we experience at high altitudes.
TPO is also highly reflective, which can help to reduce heat absorption on the roof surface and improve the overall energy efficiency of your building. By reflecting sunlight and heat away from the building, a TPO roof can help to reduce cooling costs and maintain a more comfortable indoor environment, even during the hottest summer months.
This is particularly important in Denver where our high altitude means that we have more intense sunlight and solar radiation than many other parts of the country. By installing a TPO roof with a high Solar Reflectance Index (SRI), you can take advantage of this increased solar radiation to reduce your building’s energy consumption and carbon footprint.
We have extensive experience installing TPO roofing systems on commercial buildings throughout the Denver area, and we know how to design and install these systems to maximize their energy efficiency and UV resistance. We use only the highest-quality TPO membranes from trusted manufacturers, and we follow best practices for installation and maintenance to ensure optimal performance and longevity.
When we work with clients to select a TPO roofing system for their building, we take into account all of the unique environmental factors that can impact its performance, including altitude, solar radiation, and weather patterns. We also consider the specific needs and goals of the building, such as energy efficiency targets, sustainability initiatives, and budget constraints.
We develop a customized TPO roofing solution that is tailored to the specific requirements of your building and optimized for the unique environmental conditions we face here in Denver. This may include features such as thicker TPO membranes, additional insulation, or specialized reflective coatings to further enhance energy efficiency and UV resistance.
With my expertise and experience in the Denver commercial roofing market, you can trust that your TPO roof will be designed and installed to the highest standards of quality and performance, and will provide you with years of reliable, sustainable protection for your investment.
Maintenance and Inspection of TPO Roofing
I can’t stress enough the importance of proper maintenance and regular inspections for your TPO roofing system. Our unique climate in Colorado, with its intense UV exposure, frequent hailstorms, and heavy snow loads, makes this even more critical.
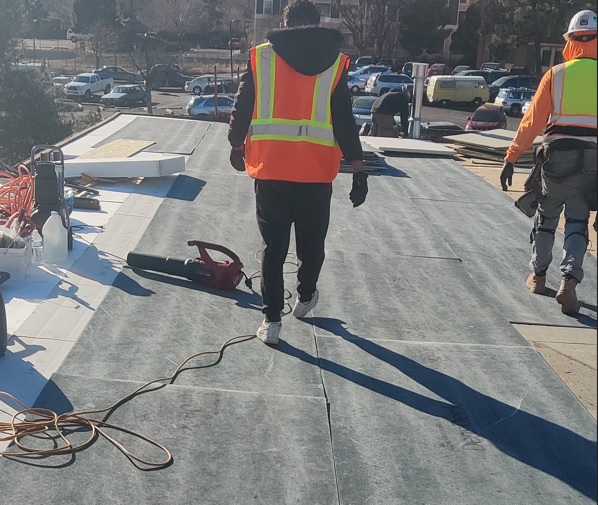
Routine Inspections
We recommend scheduling routine inspections at least twice a year – typically in spring and fall. During these inspections, my team and I meticulously examine key areas of your roof, including seams, flashings, drains, and any areas around rooftop equipment. We’re looking for any signs of wear, damage, or potential issues that could lead to leaks or other problems.
Preventive Maintenance
Preventive maintenance is also crucial for extending the life of your TPO roof. This includes regular cleaning to remove debris, which can accumulate and potentially damage the membrane, especially after our strong Denver winds. We also address any small tears or punctures promptly, using specialized techniques to ensure the repairs are effective and long-lasting.
Handling Repairs
When it comes to handling repairs, early identification is key. Our experienced team is trained to spot even subtle signs of damage that might escape an untrained eye. We use a variety of repair techniques, depending on the nature and extent of the damage. For minor issues, we might use TPO patches or sealants. For more significant damage, we might need to replace sections of the membrane.
Proactive
By staying proactive with maintenance and addressing issues early, we can help you avoid costly repairs down the line and significantly extend the life of your TPO roof. Remember, in our challenging Denver climate, regular care isn’t just recommended – it’s essential for protecting your investment and ensuring your roof continues to perform optimally year after year. Let’s work together to keep your TPO roof in top condition, ready to withstand whatever our Colorado weather throws at it.